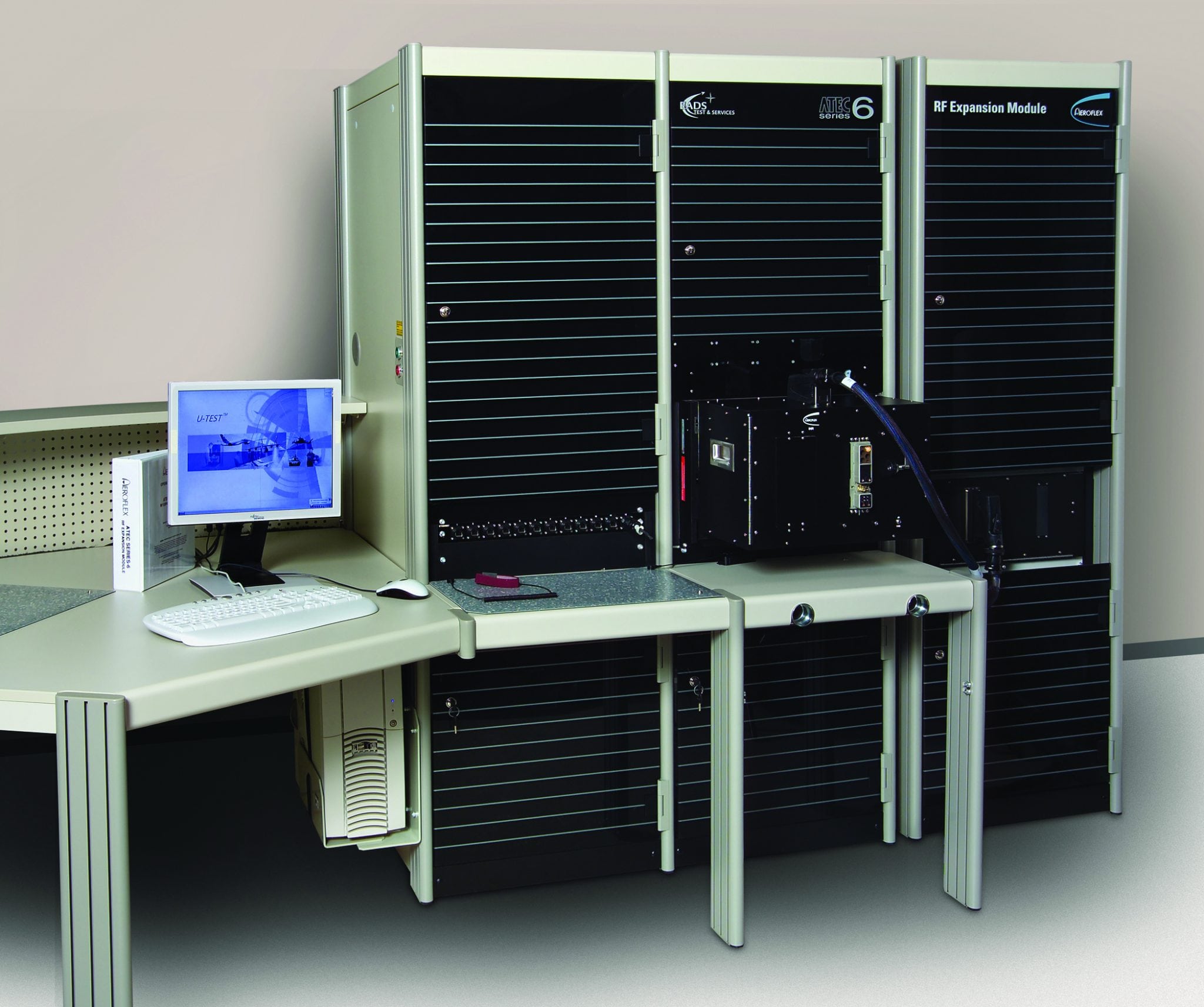 |
The Aeroflex RF Expansion Module is developed and manufactured by Aeroflex Test Solutions in partnership with the Test & Services activities inside Cassidian. The system is designed to support testing of airborne RF components on the Cassidian ATEC Series 6 ATE. |
The U.S. military services are pressing ahead with efforts to deploy and update their family of standardized automatic test systems (ATS) despite the challenging budget environment. Last year, the Army launched initial low rate production, for example, of its Next Generation Automatic Test System (NGATS), which is slated to replace older integrated family of test equipment (IFTE) over the next few years; at the same time, the Navy is adding technology to its Reconfigurable Transportable Consolidated Automated Support System (RTCASS). As they update the systems, the services’ key challenge is to field and maintain standardized testers that are capable of handling new and legacy aircraft technologies.
Introduced more than two decades ago, these standardized or common core systems each of which contains automatic test equipment (ATE), operating software and test program sets (TPS) are continuing to evolve. Over the last few years, the Navy’s Consolidated Automated Support System (CASS), one of the earliest systems, has not only added RTCASS but is also itself is being upgraded into the new eCASS program. Meanwhile, the Air Force is more than a third of the way to deploying the 150 Versatile Depot Automatic Test Stations (VDATS) it planned to have in place by FY 2017. Although critical to the maintenance of a wealth of weapons systems, these tester programs are not immune to budget cutting, but with a stated primary goal of reducing the cost of ownership of DoD ATS, they would seem to be very much in sync with the efforts to trim Defense spending.
However, the across-the-board sequester cuts could throw a wrench in development plans, but “so far sequestration has had minimal impact on FY’13-budgeted activities,” said Chris Clendenin, director of Boeing Defense, Space & Security Support Equipment & Services. Boeing is the prime contractor for RTCASS, a readily deployable version of CASS that is being produced to support Marine and U.S. Special Operations Command V-22 as well as USMC EA-6B, F/A-18 and AV-8B. Until the company receives “specific guidance from our defense and government customers … we will continue on the course we have been following for sometime as we anticipated defense cuts even before sequestration became the concern,” said Clendenin. “Boeing continues to invest heavily in R&D in spite of DoD budget constraints; we are not hunkering down.”
This guarded but positive outlook is shared by many in the industry. “Although overall spending will be reduced, we still see opportunities in niche sections of the military market,” said Barry Beasley, assistant director of the Avionics Business Unit at Plainview, N.Y.-based Aeroflex Test Solutions.
The broader effects of tighter budgets, however, do underscore the complexity of the tasks these standardized test systems take on. “Any budget-constrained environment encourages the services to think closely about the ‘sustain versus procure’ decision,” said H. Byron Green, senior director test and electronic warfare at AAI Test & Training. The company provides the Joint Services Electronic Combat System Tester (JSECST) program, an ATS that offers end-to-end testing capability to Navy and Air Force customers. The standardized testers must be able to handle not only the latest technology but also older systems on legacy platforms that have continued to operate beyond their expected operational lifetime under service life extension programs (SLEP). Last year, for example, the Air Force announced plans to upgrade and extend the service life of more than 300 F-16s and the Navy did the same for 150 F/A-18s, due mainly to delays in deliveries of F-35s.
“The services generally understand and embrace the advantages of extension programs in terms of affordability and capability; with the same footprint and a modest investment, equipment can be maintained for even decades of additional service,” said Green. SLEPs also can provide “improved performance” and add “new capabilities” to the aircraft to help “mitigate costly issues associated with obsolescence,” he said.
As platforms are upgraded, “obviously the test equipment needs to be upgraded as well … to accommodate or be able to test the newer systems,” said Mike Pefley, director, business development, Land and Self Protection Systems Division at Northrop Grumman. “These newer systems are tending toward (use of) some of the (newer) interface standards” such as PXI and VXI, he said. Those standards simplify the task “because when you have standard then it just makes it more straightforward” with less need for customization.
As they develop new automatic test equipment for the systems or subsystems, technology providers are accounting for the need to support legacy and new systems along with customer demands for greater efficiency and flexibility. “We continue to see emphasis on multi-function capability, (such as) combined instrumentation and software-reconfigurable systems,” said Green. For example, “the radio frequency sources we have supplied for our major U.S. Navy and U.S. Air Force programs offer ‘forward/backward’ capability external and embedded modulation enables compatibility with both legacy and future systems.” The company is also working on several new electronic warfare products, Green said. Priorities include “systems that provide full electromagnetic environment simulation, ‘forward/backward’ system support, integrated frequency and time domain analysis, and consolidated support across all radio frequency sources.”
“Customers are (also) demanding more compact test systems with lower cost of ownership; there is a general move away from ‘rack-and-stack’ solutions, which have a higher cost of ownership,” said Beasley. For example, Aeroflex offers its IFF-7300S, which supports IFF Transponders/Interrogators and TACAN Interrogators and can be customized to meet individual under test requirements, he said.
In addition, the company is “continuing to add new capability to the RF Expansion Module for the Cassidian ATEC Series 6 (ATE),” Beasley said. “This is a new platform for us, so there is a lot of focus on growing our offered TPS library; we have several TPS developments currently in process with numerous in the planning stages,” he said. “The ATEC series 6 provides test coverage for every major airborne avionics equipment manufacturer on the Airbus, Boeing and ATR aircraft as well as numerous military aircraft,” according the systems manufacturer, Cassidian, an EADS subsidiary.
“In the area of Flight Line test equipment we see little difference between testing older, upgraded military platforms compared with new military platforms,” said Beasley. Addressing older systems, “we have standard support commitment period after a product reaches the end of its production life,” he said, adding “we are still supporting … some test instruments that are 25 + years old.” However, “a continuously reducing pool of vendors for legacy components and general component obsolescence creates an ongoing support challenge, which is the situation of every manufacturer in the aviation industry.”
 |
AAI’s Advanced Architecture Phase Amplitude and Time Simulator is designed to verify that U.S. and allied aircraft electronic warfare systems can locate, identify and defend against ground-based and surface-to-air missile threats. |
When it comes to developing or expanding automatic test systems, a key solution for integrating legacy test equipment is TPS transport or migration technology that allow for “moving TPSs from one platform to another without changing the TPS hardware or software,” said Clendenin. Currently several ATE programs are capitalizing on this technology to boost cost savings by “extending the useful life and reducing development costs of TPSs,” he said. This year, Boeing and the U.S. Navy successfully completed the transport of more than 650 TPSs from the legacy CASS to RTCASS for use by the Marine Corps in support of F/A-18C/D Hornets, H-1 Cobras, AV-8B Harriers, E/A-6B Prowlers and MV/CV-22 Ospreys.
In 2012, the U.S. Navy contracted with Boeing to develop the RTCASS depot for the North Island Fleet Readiness Center. “This new variant of RTCASS will incorporate new technologies to enable testing of shop repairable assemblies and reduce TPS development costs,” said Clendenin. The system, to be delivered in 2014, will allow for “the use of Test Stand and Lab Windows CVI for TPS software development and (include) new capabilities in … digital testing, analog testing, as well as a new control computer,” he said.
Boeing is also “continuing to expand development and deployment of toolsets designed to collect, process and share information with the operations and maintenance communities,” said Clendenin. “These toolsets facilitate secure communications and data exchanges as well to enhance various elements of health management, both on and off-weapons system,” he said. “Within the past year we have started to incorporate our net-centric toolset into the DoD’s next generation of operations management software; this effort is leveraging the DoD’s existing network security infrastructure to ensure secure cross-domain data exchange.”
Last year, Northrop Grumman, along with DRS Systems, delivered eight Next Generation Automatic Test Systems under a low rate initial production contract with the Army. NGATS is slated to replace the service’s legacy integrated family of test equipment (IFTE) and Direct Support Electronic Systems Test Set (DSEST), said Pefley. This ATS adds new capabilities and has a smaller footprint than the legacy systems and is a reconfigurable, modular solution that offers VXI instrumentation for flexibility and rapid insertion of future technologies, according to Northrop Grumman. Over the next few years, NGATS “will be capable of assuming all current and projected ATS missions,” according to the DoD Automatic Test Systems Executive Directorate. Under current plans, the ATS capabilities will be deployed gradually via a spiral development process allowing for “the planned incremental replacement of aging ATS experiencing increasing obsolescence issues.”
Currently, the eight LRIP systems along another eight delivered during the test phase of the program “are in trials and in use and with the Army,” said Pefley, adding “at this point we are preparing for the full rate production phase of the program.” The service is expected to issue a RFP this year for full rate production of about 42. “We look forward to that competition and feel like we are very well positioned to participate and support the Army,” he said.
To this point, automatic testers are not generally being used for the systems on unmanned aerial systems (UAS). However, “the replacement value of all unmanned aircraft has increased,” said Green. “I expect this trend to continue as even more powerful and complex payloads, communications and other subsystems are integrated in all UAS classes,” said Green. “As cost, complexity and miniaturization continue to increase, so does the need for robust test capabilities.“
In some cases, testers are already being used to maintain those sensors that are common to both unmanned and manned systems, added Pefley.
New standards, such as Future Airborne Capability Environment (FACE), crafted by government and industry “will help reduce the cost of new systems and their associated tests, but the legacy systems will still be in use for many years,” said Clendenin. “We believe that the implementation of FACE will present a challenge in order to integrate these new technologies while maintaining compatibility with legacy systems.” Meanwhile, “the DoD has been studying the concept of a new common development environment for test that may replace legacy approaches,” said Clendenin. “This future environment would be based on a common test executive and enable use of multiple runtimes, common TPS procedures, and standardized tool sets for graphics and test diagrams.”
Looking forward, the DoD Automatic Test Systems Executive Directorate said last year new ATSs may be added to the DoD inventory of ATS families if they meet the following criteria:
➤ The tester must be capable of supporting multiple weapon system test requirements and there must be planning in place for implementation as such,
➤ The tester must have flexible hardware and software architectures which are expandable and tailorable with minimal impact to existing logistic support profiles and TPSs,
➤ The tester must provide a capability to satisfy a Service performance or operational requirement that cannot be accommodated within the existing DoD ATS family structure,
➤ The tester must provide a more cost effective/beneficial ATS solution than use or modification of an existing DoD family member, and
➤ The tester must be re-procurable and must have a dedicated government management office that has a process in place to ensure long term tester viability is maintained; and the tester will evolve to satisfy future support requirements.
Next month: Electronic Flight Bags
Avionics Magazine’s Product Focus is a monthly feature that examines some of the latest trends in different market segments of the avionics industry. It does not represent a comprehensive survey of all companies and products in these markets. Product Focus Editor Ed McKenna can be contacted at [email protected].
Marvin Test Solutions Bullish on Defense
While cuts in U.S. defense spending are causing angst in much of the aerospace industry, Steve Sargeant, CEO of Marvin Test Solutions, sees opportunity there.
Since the Department of Defense cannot afford to replace many of its aging aircraft, it is upgrading them with smart weapons and other technology so they remain relevant in modern warfare and can stay in service far longer than expected, which will create a need for reliable and robust test equipment systems.
Marvin Test Solutions, formerly Geotest-Marvin Test Solutions, builds test equipment for legacy as well as new aircraft. In an interview with Avionics, Sargeant explains how Martin is well positioned for today’s austere fiscal environment.
Question: What are some trends that you’re seeing in the aerospace test equipment market? How is your company responding to those trends?
Answer: Our customers have to sustain legacy aircraft longer into the future. In many cases, those legacy aircraft were upgraded over the last few years. For example, smart weapons were added to the A-10. But the test equipment didn’t change, and so today, in the case of the A-10, they find themselves without any smart weapons test equipment on the flight line. The A-10 is operating with test equipment that was fielded many decades ago, and the aircraft has so much more capability that can’t be trouble shot, that can’t be maintained on the flight line.
So the opportunity that we see is now going to the Air Force and presenting a technology that increases the capabilities while at the same time decreasing the footprint on the flight line. We don’t want them to discover they have a problem after they’ve loaded up a 2,000-pound weapon onto the aircraft. It’d be great to know beforehand if there’s any troubleshooting to be done.
Q: Do you see opportunities in unmanned aircraft systems?
A: Unmanned aerial systems is a very exciting market. I think it’ll be a growing market in the future, both in defense and civil and commercial, and probably in that order. There are opportunities today for the use of test equipment on the UASs that are being deployed to ensure that the armament and ammunitions are working properly before those UASs launch on their missions.
We are working closely with the manufacturers of UASs today and the users to see if they’re interested in this type of support equipment, and we think they’re. And we’re making our systems available to them and knowledge of our systems widespread.
For future systems, if those systems are going to be using armament to enable carriage of sensors, etc., and the sensor packages themselves, they also provide opportunities for test systems, test solutions to be employed. So we’re keeping a close eye on that market, and its not a passive eye, it’s a very active eye, we engage with the manufacturers and the users daily and will continue to do that.
Q: What does the next 12 to 18 months look like for your company?
A: We’re on a growth path right now, and despite sequestration and the doom and gloom that folks see from other sectors of our industry, we see opportunities there, and we see great reception from our customers because of the solutions we can bring them to help solve their problems of long term sustainment, while at the same time they’re facing bringing on new fifth-generation systems like the F-35, we’re able to help at both ends of the spectrum. So we’re actually growing because of some of the people that we’re actually bringing on and some of the projects that we’re winning.
We look forward to continuing winning more and continuing our growth. —Woodrow Bellamy III