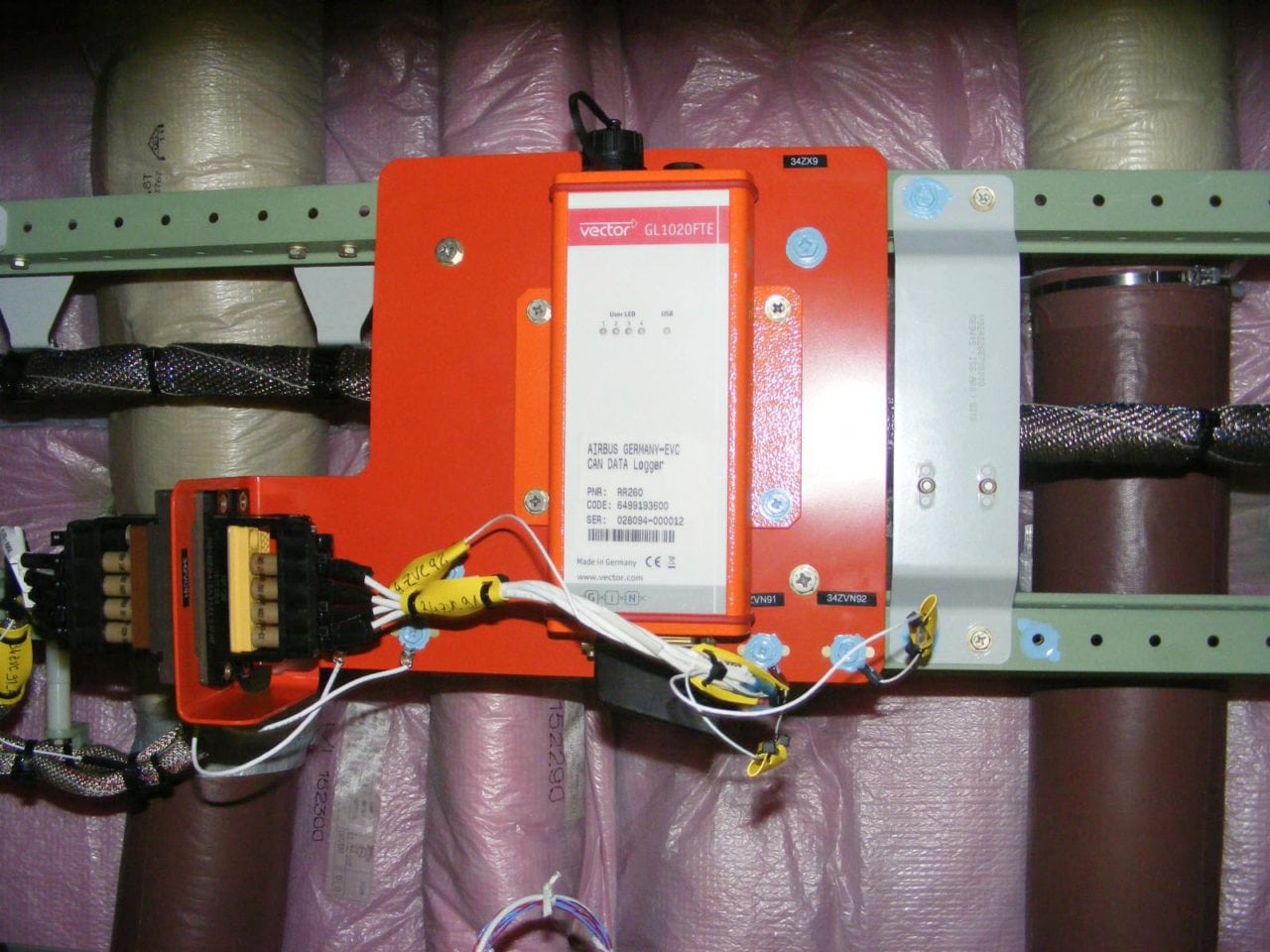 |
Vector’s CAN bus data logger. Photo: Vector |
[Avionics Today 10–28-2014] Airbus, in need of a unique device for cabin test activities on their A350 XWB test aircraft, asked Vector to build a mobile Controller Area Network (CAN) bus data logger. In February 2014, the German software developer completed its first test trial of its GL1020FTE data logger analyzing CAN data bus communications onboard the second flight test aircraft of Airbus A350 XWB, equipped with a full test cabin.
“Normally in a flight test aircraft like the A350 [XWB], they get huge flight test installations to test, log and analyze a lot of data on the aircraft — data from avionics, structural data and so forth,” said Arne Brehmer, director of Vector’s aerospace customer center in Hamburg, Germany. “But these flight test installations don’t test every data of these special cabin systems. Airbus came to us and asked us to build a data logger that is quite small, mobile and that they can equip fairly quickly.”
A CAN data bus is a serial communication protocol for a reliable, simple and cost-efficient data exchange between electronic units, first introduced for Mercedes-Benz cars in the 1990s. It is used extensively by Airbus for cabin testing in its A350 XWB to reduce the number of interconnected wires from control panels in the flight deck to system computers in the avionics compartment. With the GL1020FTE data logger, Vector aims to make collecting and analyzing data for the three cabin systems involved — galley, water and waste, and auxiliary heating — easier, faster and, above all, smaller.
Vector began building the data logger to the requirements of Airbus and RTCA DO-160E standards — the special qualifications of airborne equipment for vibrational shocks and environmental conditions such as humidity. However, the system also meets typical avionic requirements on electromagnetic compatibility (EMI) suitable for the A350 XWB’s composite fuselage.
The result is a portable data logger that can be placed almost anywhere in the fuselage of nearly every aircraft system that is in a pressurized area, according to Brehmer. It can time-synchronously record up to 32 gigabytes of data from two CAN channels and four analog measurement channels and is interoperable in aircraft with CAN networks including galley, water and waste, environmental control and de-icing systems.
“The intention is that these data loggers can be used for other aircraft types like A340, A330 and the A380,” Brehmer said, noting that the logger isn’t confined to the flight aircraft for which it was built.
And while Airbus has been the only manufacturer using the system so far, Brehmer envisions a much larger market.
“It can be used for other aircraft, like Boeing, Bombardier or Embraer, as well. Boeing’s Dreamliner has a lot of CAN bus in the aircraft and so this would be a good system for testing that,” Brehmer said, noting that the logger can only be used on aircraft where the CAN-networked systems are integrated and would also require checking and fulfilling the specific flight test requirements of the individual manufacturer.
According to Vector, the system provides offline bus analysis in tools such as CANoe, CANalyzer, CANape and CANgraph, among other features, and is operational up to 36,000 feet. Multi-bus systems with AFDX and ARINC 429 can also be tested efficiently.
“The unique point of our system is that it’s really small,” said Brehmer. “So it’s possible to have a small, mobile solution to put somewhere in the fuselage with the opportunity to have really powerful software tools behind it.”