Developers of databus test equipment are feeling the pinch as new commercially developed technologies that aim to boost throughput and lower costs begin to enter aircraft, adding complexity to platform architectures and equipment. Aircraft operators and owners are beginning to equip with new technologies such as those that aim to supply the Ethernet data rates needed to run In-Flight Entertainment (IFE) systems, which use emerging avionics bus technologies, like Fibre Channel (FC), MIL-STD-1760, and ARINC 664/AFDX, alongside legacy systems that continue to use ARINC-429 or MIL-STD-1533 buses.
With new systems being introduced every day, nearly three-quarters of respondents — 72 percent — to our 2015 Avionics Databus Test Equipment survey expressed the need to acquire new databus testing equipment. The main driver of this demand is the need to test systems integration as new aircraft systems are introduced alongside legacy equipment, closely followed by the need to satisfy a service performance or operational requirement, such as a mandate.
In choosing which databus test equipment to purchase, an overwhelming 72 percent of respondents noted that the ability to test both legacy and next generation systems together were the main concern, with the ability to provide multifunction capabilities, such as testing combined instrumentation and software reconfigurable systems, coming in at a close second with just under 50 percent of respondents marking this as the main driver in their decision-making process.
“Like many industries, the avionics industry has been tasked to do more with less in a number of ways over the last five years — and the pressure to do this has intensified over the past two to three years. The situation is exacerbated by the growing complexity of aircraft systems, and the capabilities of the aircraft systems and add-on mission systems are being tasked to do much more than they used to do in the same place,” explains Bill Tilman, avionics application engineer at GE Intelligent Platforms.
To compensate for the new challenges and increasing complexity in platforms, vendors are introducing an array of solutions that will help manage the data flow between new and legacy buses while still addressing size, weight and power limitations. But these issues are further complicated by economic circumstances putting the squeeze on manufacturers.
Ethernet: Enabling IFC and IFE
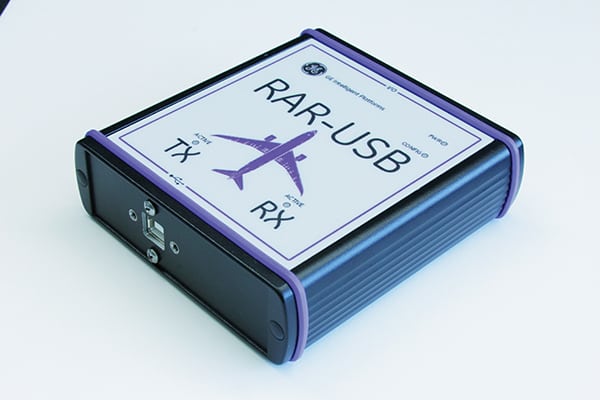 |
The GE RAR-USB ARINC 429 USB Adapter, which is designed for users to test ARINC systems and for debugging, monitoring and analyzing bus traffic and data recording and can be used with Windows XP onwards. Photo courtesy of GE Intelligent Platforms. |
In commercial systems, the rapid adaptation of In-Flight Connectivity (IFC) and In-Flight Entertainment (IFE) systems are generating a complicated landscape for databus test system designers and manufacturers.
Mirko Jakovljevic a solution architect of integrated critical systems at TTTech, a manufacturer of deterministic system integration and advanced embedded platforms for the aerospace industry, confirms the rising interest in Ethernet-based solutions in aircraft. “We see a clear shift towards applications with the need for high-bandwidth networking architectures that exceed the capabilities of bus-based solutions. This need for high-bandwidth can only be satisfied by deterministic Ethernet,” says Jakovljevic, referring to the new AFDX databus.
“As an example, deterministic Ethernet is about to trigger a new evolution of high-volume automotive systems and ADAS [Advanced Driver Assistance Systems]. This can also influence future aircraft systems such as IFE and IFC,” Jakovljevic adds.
In particular, Jakovljevic finds that TTTech’s customers are intrigued by the ability to integrate critical and non-critical functions on one physical network. With integrated systems, the design assurance for embedded platforms and network devices becomes more important in order to minimize integration effort and costs, which can be done with deterministic Ethernet solutions that aim to simplify point-to-point — endstation-to-switch and switch-to-switch — connections within a fuselage. This configuration enables a higher performance for networks in comparison to databuses that have many units broadcasting over one physical layer.
“Deterministic Ethernet-based architectures reduce the physical complexity of the system by taking away the need for using multiple, physically separated, data buses. This directly addresses the [Size, Weight and Power] SWaP reduction demands from the industry but requires more sophisticated methodology and processes when designing complex integrated architectures,” Jakovljevic explains.
Until the entire aircraft system can rely on deterministic Ethernet, the company is looking to address the need to manage the flow of data between new and legacy buses with new software, such as TTTech’s AeroQ, which is an advanced DO-330 qualified tool for formal proof of heterogeneous aerospace networks like ARINC 664 part 7, ARINC 429 and ARINC 825. “We believe that tools like this are vital for helping the industry make the transition away from legacy buses to an all Ethernet aircraft,” says Jakovljevic.
Evolving Systems
 |
XMC card for Embedded ARINC429 interfaces. Photo courtesy of AIM. |
With new digital architectures for aircraft avionics constantly evolving, companies are introducing new databus testing applications to support systems integration.
“Testing and simulation tools are constantly growing and evolving to meet customer demands for easier development of, and visibility into, aircraft buses,” explains GE’s Tilman. “If anything, we’re seeing increasing demand from custom solutions to address this growing complexity.”
To address this, GE is continually adding new features and functionalities to baseline tools.
The company also looks to address the increased life cycles of aircraft systems and test equipment, as the test systems, production test equipment and Software-In-The Loop (SIL) systems remain in use for longer. These new systems require developers to inject a more flexible and open approach to systems in the test equipment architectures as they aim to keep legacy equipment alive for longer in the face of shrinking budgets.
“GE responds to these extended life cycles through the use of [Field-Programmable Gate Array] FPGA technology updates of our test equipment interfaces. This enables our customers to add new or customer functionalities over time, without changing the qualified test system (which is extremely costly to do), prolonging the lifetime of the test system while maintaining cost,” Tilman adds. This same thinking applies to systems software, which Tilman identifies as one of the most challenging aspects of most aviation simulation systems. While the system is required to change for safety and security reasons, companies are striving to ensure minimal changes to the user interface after an upgrade.
Doing More with Less
Alongside the new complexity and financial challenges, manufacturers are, as always, seeing an increased demand for solutions with reduced Size, Weight, Power and Cost (SWaP-C).
“In general, test equipment manufacturers have looked for ways to integrate more functionality and higher channel density into a smaller footprint at the equivalent or reduced cost,” says Sean Sleicher, director of business development at Holt Integrated Circuits.
This is a trend that has been fed by the transition from 5V to 3.3V databus components and the increased desire for portable test and monitoring equipment. New products, such as the Aircraft Interface Device (AID) aim to address this complexity and manage the data flow, while still addressing SWaP-C.
“The AID acts as a firewall device between critical and avionics networks and non-critical networks not approved to control avionics equipment. Holt’s HI-3200 ARINC 825 (CAN) ARINC 429 bridge IC allows communication between legacy ARINC 429 networks and newer ARINC 825 networks used in non-critical areas such as galleys and washrooms,” says Sleicher.
Other companies are cutting down through configurations that use very small and low-power form factors. AIM uses its USB-based Smart Cable product, “which now have the ARINC 429 or MIL-STD-1553 Databus Analyzer electronics integrated into an industry standard D-Sub connector, all the way up to the PXI/PXIe (3U), CPCI (3U) or VME card formats for more complex applications,” to cut down on power, according to Douglas Ullah, director of sales and marketing at AIM.
Manufacturers are also looking at ways to pack more functionality into a smaller form factor. Holt has addressed this need by moving to smaller geometry Integrated Circuit (IC) technology, according to Sleicher, who identifies the task of increasing functionality within a smaller space as the company’s greatest challenge. By moving to smaller IC tech, Holt has enabled the footprint of its MIL-STD-1553 protocol ICs to shrink by 56 percent in the last five years.
Minding the Military
Both the military and commercial aerospace sectors are seeing increasing complexity that requires manufacturers to introduce new types of interfaces to testing tools to provide the ability to tie together and synchronize multiple protocols. While the commercial sector is seeing a steep amount of development, however, military spending restrictions are still limiting a certain amount of development.
Increasingly, to keep costs down, military operators are turning toward Commercial-Off-The-Shelf (COTS) technologies. Large parts of the military continue to invest a significant amount of development and integration in COTS technology solutions for their embedded computing needs, based on open, industry standards and commercially available technologies,” explains Tilman. GE is seeing a move toward technologies such as Ethernet, Controller Area Network (CANbus) and a combination of protocols in test systems. He is also seeing a greater need for portable systems, which allow avionics companies to leverage their assets more effectively and is driving the advent of higher density, multi-card protocols.
“The migration of COTS backplanes (such as PCI to PCIE) and operating systems (such as Windows XP to Windows 10) relentlessly continues, which drives constant development as we make our test products available for various hosts, “ he says. “This move over many years has certainly helped provide new capabilities and innovations to avionics systems.”
Up and Up: Soaring Certification
While manufacturers of databus test equipment are battling new cost and size requirements alongside more complex architectures, swelling certification is also presenting an issue with shifting designs.
“[We have] observed an increase in certification requirements with standards like DO-254 or DO-178 becoming more commonplace,” explains Holt’s Sleicher. “Along with the increase in certification requirements comes new testing philosophies, whereby a design must be rigorously tested to make sure it meets every one of its design requirements. This can become very complicated and costly in the case when implementing a databus protocol in an FPGA [Field-Programmable Gate Array],” says Sleicher, speaking to an integrated circuit that is designed to be configured by a customer or a designer after manufacturing.
To combat complexities from increasing certification, Holt and other companies can supply documentation with protocol systems that aim to enable customers to certify systems with less effort.
XMC card for Embedded ARINC429 interfaces. Photo courtesy of AIM.The GE RAR-USB ARINC 429 USB Adapter, which is designed for users to test ARINC systems and for debugging, monitoring and analyzing bus traffic and data recording and can be used with Windows XP onwards. Photo courtesy of GE Intelligent Platforms.
Juliet Van Wagenenis the assistant editor for Avionics Magazine.