[Avionics Today 07-06-2016] Coming off a record year in revenue in 2015, Canadian avionics manufacturer Flyht Aerospace’s first six months of 2016 point to another big year for the company that has made the streaming of Flight Data Recorder (FDR) parameters a reality. Avionics Magazine recently caught up with Flyht Aerospace CEO Thomas Shmutz and Chief Technology Officer (CTO) Derek Graham to discuss how the company’s Automated Flight Information Reporting System (AFIRS) technology will be migrating from terrestrial to cloud-based servers. The executives also discussed Flyht’s partnership with a post-flight data analytics company as well as recent examples of operators cutting costs using its real-time Aircraft Health Monitoring (AHM) capabilities.
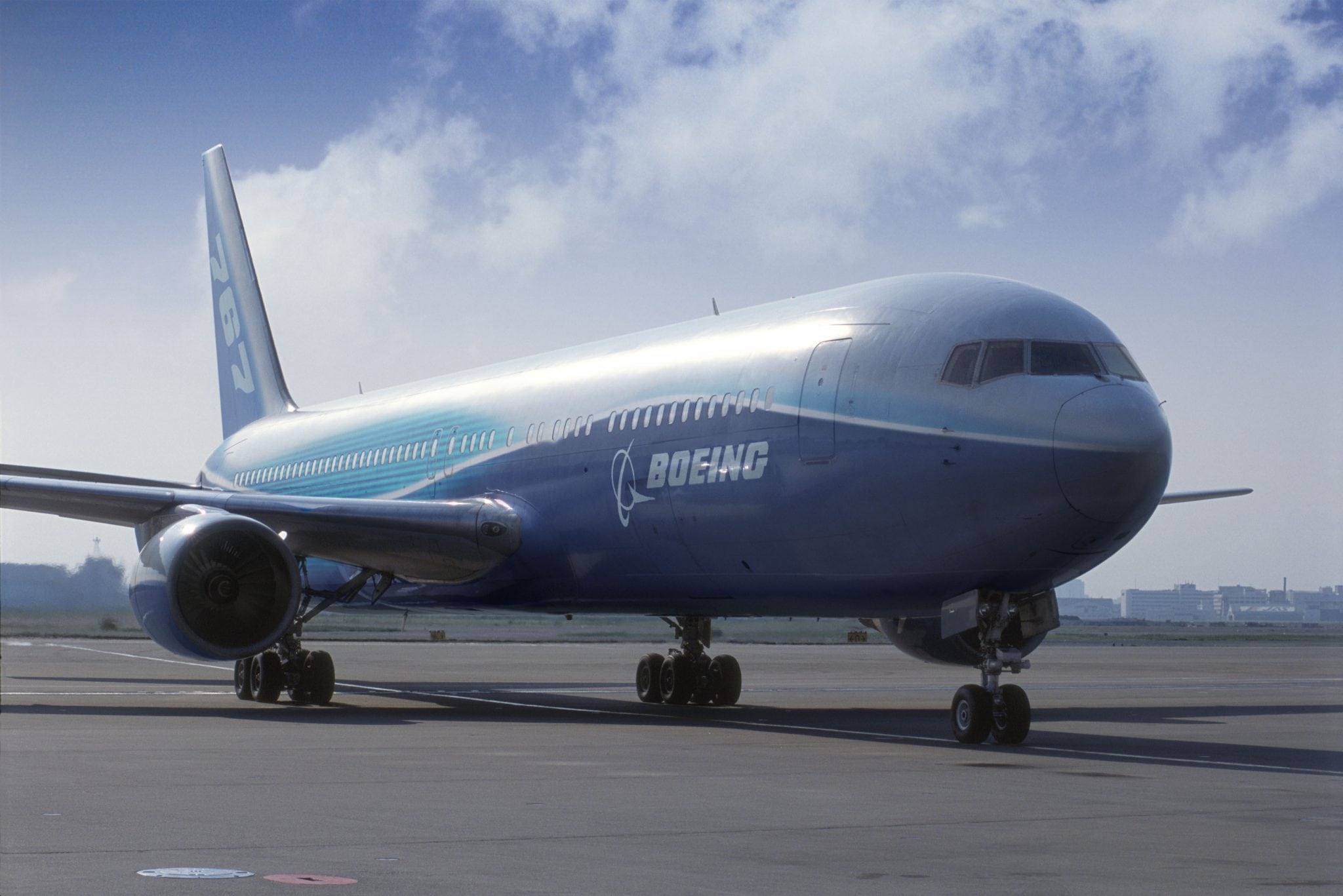
A Boeing 767-300, one of the recent aircraft types Flyht achieved an STC on. Photo: Boeing.
Through the first six months of 2016, Flyht has earned Supplemental Type Certificates (STCs) for AFIRS on six different air transport category aircraft types. By the end of 2016 a total of 10 new aircraft will enter into service with AFIRS 228 onboard, demonstrating industry demand for the capability that it can provide. In the second quarter of 2016 the company also signed three new airline contracts for AFIRS-powered voice and data services. The technology also recently received an STC for the system from the Civil Aviation Administration of China (CAAC) for the Boeing 767-200 and 300, specifically for an unnamed Chinese airline that is operating AFIRS on five different Boeing 767s.
Flyht’s blue AFIRS 228 box uses two Iridium channels, with one transceiver providing global voice and data communications, and a second modem dedicated to datalink services using standard Aircraft Communications and Addressing Reporting System (ACARS) and Future Air Navigation System (FANS) message sets. The second part of this equation is Flyht’s ground-based server interface, UpTime, which captures data produced by AFIRS and then can immediately notify key personnel through email or text-based alerts about engine exceedances and other important aircraft health data. Graham says the proprietary software Flyht uses is the key to the ability of AFIRS to stream FDR data in real time.

AFIRS 228. Photo: Flyht Aerospace.
“The onboard Embedded Launching Application (ELA) is Flyht’s proprietary software that resides in the AFIRS box, and it determines–based on the customer’s requirements — what information you want to capture about the aircraft performance, how much information you want and when you want to send that information to the ground. Software is able to identify what data you want. To address bandwidth issues, it compresses all of the data to reduce the cost of the data transmission itself. Then we send that data out to the Iridium satellite system, down to the gateway and then to the UpTime Server that’s when we unzip the data, we put it back in order and then we put it in formats that are specific to the customer’s needs. It’s the actual software that we have that makes the FDR live blackbox streaming very easy for Flyht,” said Graham.
In a recent letter to shareholders, Schmutz described how that software saved one particular airline $4.42 million by preventing them from making an unnecessary engine replacement. The airline, which wished to remain undisclosed, had recently purchased several used Boeing 767 aircraft.
After only two weeks in service, according to Schmutz, the AFIRS system reported turbine vibration exceedances in one of the engines of the 767. AFIRS was able to detect this abnormality because of its ability to monitor onboard sensors and compare this data in real time against limits, which can be set according to the Original Equipment Manufacturer (OEM) specifications or the airline’s own thresholds.
Next, in an effort to establish an early detection of potentially serious problems, the airline deliberately set the limits below those established by the engine manufacturer. As a result, UpTime reported each exceedance within seconds of occurrence to the operator’s maintenance personnel. These reports resulted in the engine being placed on a watch status for subsequent flights. The airline was then able to determine that the turbine vibration was increasing, and it was pulled out of service where the maintenance personnel found that the engine was close to committing a turbine failure because of a mechanical flaw. Instead of completely replacing the engine for $5.2 million, it was repaired for $780,000 and returned to service.
A partnership announced earlier this year between Flyht Aerospace and Flight Data Services (FDS) was established to satisfy another demand the company had been hearing from its existing AFIRS customers: post-flight analytics. FDS’s Polaris platform can automatically translate aircraft data transmitted during a flight into a valuable set of information that an airline can use to meet international Flight Operations Quality Assurance (FOQA) regulations.
“We had a number of customers asking us whether we can offer a post-flight analytics program. Because our core competency is on real-time data acquisition and delivery, it’s not something that really we want to focus on. The natural progression for us was to partner up with a company like FDS so that we could offer increased capabilities and benefits to our existing customers. The sorts of data for the FDS is the actually AFIRS data that is contained on our 16 GB flashcard. Now our customers take that card when the aircraft lands and upload it into the Flight Data Services software for post-flight analytics,” said Graham.
Now, with STCs covering nearly 95 percent of aircraft used for commercial air transport today and AFIRS 220 and 228 achieving more than 2.2 million flight hours on more than 1.4 million flights, Flyht’s chief executive said the company’s focus going forward is to transition its real-time data acquisition service to a cloud-based environment.
“We are in the process right now of migrating it from a fixed server to a cloud-based server, and that’s a product that we’re going to be launching formally later in the year. We have it running now with two clients and getting ready to run it with a third,” said Schmutz.