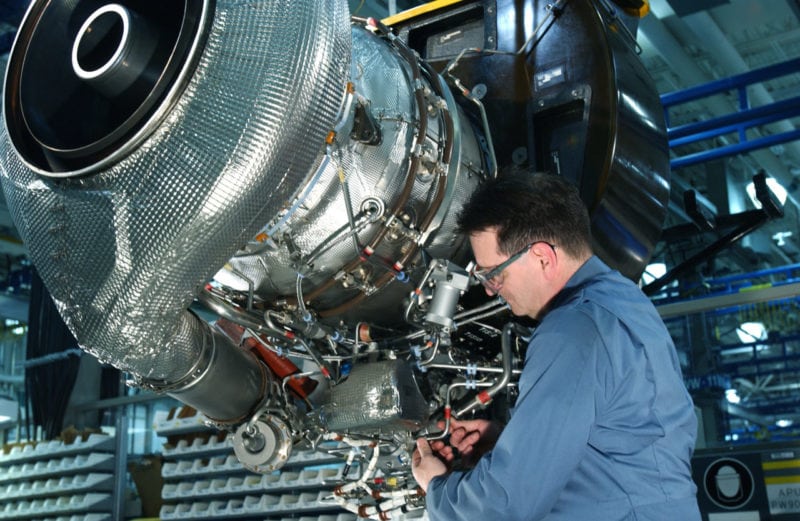
A technician works on a PW901 engine. Photo: Pratt & Whitney Canada.
Aircraft engine health monitoring is one of the most critical activities for every business, commercial and military, fixed- and rotary-wing operator looking to predict current and future maintenance needs across their fleets.
Several years ago, Pratt & Whitney Canada introduced its Flight Acquisition Storage and Transmission (FAST) system, designed to capture and analyze engine and aircraft performance parameters. When an aircraft equipped with Pratt & Whitney Canada engines lands, the FAST system provides cellular transmission of engine and aircraft performance data from the aircraft to Pratt & Whitney Canada, where a full-flight data intelligence report is produced to provide operators with information that can improve engine maintenance predictability.
As Gulfstream prepares to enter into service what will be the industry’s most advanced corporate jet, the Pratt & Whitney’s G500, Avionics caught up with Tim Swail, VP of customer programs, and Bjorn Stickling, manager of diagnostics, prognostics and engine health management to learn about the latest connected engine capabilities available.
Avionics: Gulfstream expects to receive FAA type certification on the G500 this year, and considering the PW814GA powers that aircraft, can you give us an overview of how many engine parameters can be captured by FAST for that engine, and what type of onboard technology will enable that for FAST, considering all of the new technologies featured on the G500?
Swail: We will receive over 300 parameters directly from onboard systems that are built into the G500 enabling us to achieve equivalent automatic data capability and wireless transmission as with our FAST box. We run this data through the FAST solution backbone to our analytics platform that delivers our digital analytics and services. The solution will enable us to provide G500 customers with trending health and usage alerts when the pilot shuts down the engine to support increased availability, proactive and preventive maintenance, and optimized operations.
Avionics: For in-service aircraft equipped with P&WC engines that do not currently feature FAST data-acquisition technology, what type of modification is required to enable FAST?
Stickling: FAST is a fully integrated turnkey solution that is easy to install and retrofit, so it can quickly connect to the aircraft and record data. It replaces the need for quick access recorders and has numerous inputs and outputs enabling it to connect to multiple systems. FAST can be easily configured to different avionics inputs and engine control units. There are typically no software modifications required on the FAST controls because the solution can adapt to the different types of data streams available on the aircraft, and we can often do any configuration remotely.
Avionics: How has FAST been used to drive the concept of predictive maintenance?
Swail: We’ve had operators indicate to us as much as a 20% reduction in delay and cancellation risk through having easy and quick access to the FAST engine health data and analytics.
Avionics: P&WC recently tested a new oil debris monitoring solution currently in development. Can you give us an update on that trial?
Swail: We have over 4,000 engines in our fleet signed up to our oil analysis technology trial, which began less than a year ago and continues to build momentum as a next-generation, on-wing monitoring solution for preventive maintenance. Now in the final stages of development, this innovative oil debris monitoring technology has the potential to far exceed the efficacy of existing oil-debris monitoring methods. It is demonstrating its ability to drive increased aircraft availability and reduced costs by identifying the deterioration of specific oil-wetted components hundreds of hours before a potential event occurs — without having to remove the engine.
Avionics: Are there any new capabilities you’re researching?
Stickling: Although today FAST does not transmit data in flight, P&WC has designed the solution to segregate different data types that can be transmitted at certain stages of the flight cycle. For example, FAST is ready to adapt to satcom and send shorter bursts of data in flight while sending larger data sets through the ground-based system upon engine shutdown by the pilot.
On the more immediate horizon, we are completing final certification of our propeller-balance trending system as part of our FAST solution for regional airline customers. We expect to go into production in June 2017 on ATR aircraft and we have just installed the first system on the Bombardier Q400. As expected, we are seeing solid trend data on both aircraft applications that will allow airlines to put propeller balancing maintenance activities into “on-condition” mode for a truly optimized environment. The solution will also enable better passenger comfort, reduced operating costs and greater component reliability due to lower propeller vibration levels.