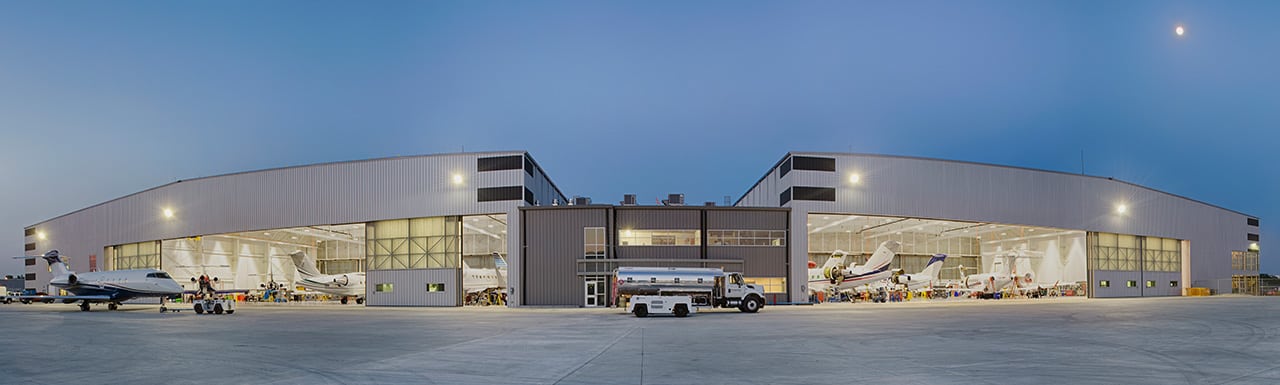
Photo courtesy of Duncan Aviation
Duncan Aviation added 3-D illustrator Dan Ryba to its in-house aircraft interior and paint design team in April. Since then, Ryba has been working with Ken Reita, another Duncan Aviation multimedia illustrator, to save the company resources, it said.
“These 3-D renderings save a great deal of time and money, so they’re popular with all of our clients internal sales and production people,” Reita said. “Unlike with 2-D drawings, we can draw from our extensive engineering database and generate accurate 3-D models of the entire interior that are specific to the actual measurements of an aircraft. You can see immediately what works and what doesn’t.”
Duncan Aviation said Reita and Ryba are focused on creating 3-D conceptual illustrations for clients looking to make interior and exterior modifications to their aircraft. Explaining with words how a design will feel to customers, for example, is not as effective as being able to show them.
“When clients look at the illustration, they might say, ‘Whoa! The darker material is too heavy for that space. Let’s go with the lighter color.’ Or, if they really want that dark color, we can suggest other options, such as going with a lighter color on the leather seats or carpet to provide more of a contrast and get the ratio of light to dark correct,” Ryba said. “It’s far better to find out on the front end before any work has been done on a project. Our clients especially appreciate being able to see exactly what they’re getting.”
The company said that customers could also request a 3-D image when a face-to-face meeting is not convenient. Duncan Aviation said the image could be included in the sales package. The company said its production teams also benefit from 3-D models when it comes to production planning long in advance.
“Recently, a client, interior team lead, engineer, salesperson and I were sitting at a conference table with a 3-D preliminary concept of a credenza cabinet,” Reita said. “Using the 3-D model as a focal point for our discussion, we went through each modification. For the cabinet, the client wanted to see where the electronics would plug in and how they’d look sitting on the shelves. The engineer looked over the model to see how to mitigate heat build-up and where to put the ventilation and wiring. The team leader wanted to make sure the cabinet shop could build the shelves and install pocket doors with the rounded edges and corners in the design. I was concerned about retaining the beauty and balance of the design. With all of our input, we figured it out pretty quickly before any production was started.”