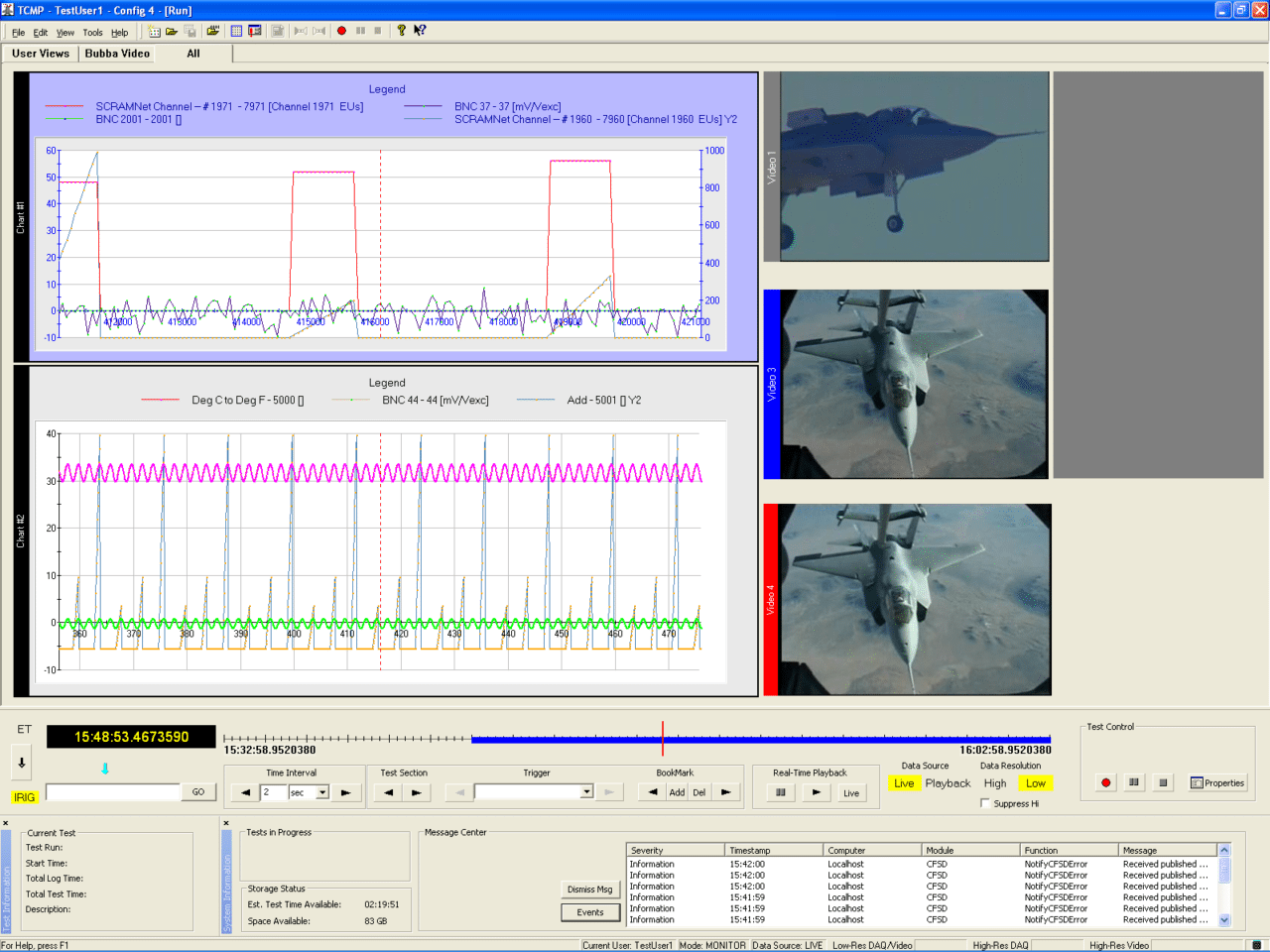
F-35 subsystem integration monitoring data acquisition system graphical user interface. Photo courtesy of G Systems
Game-changing communications, navigation and surveillance capabilities on the F-35 are powered by more than 8 million lines of code and the most advanced embedded computing power ever featured on a fighter jet. Avionics recently caught up with Texas-based engineering service firm G Systems, which developed a data acquisition system capable of monitoring data generated by F-35 sub-system integration tests.
Lockheed Martin’s F-35 Vehicle Systems Integration Facility (VSIF) presented G Systems with a data acquisition system challenge — build a needed integrated system capable of acquiring analog, digital and video data transferred from systems using reflective memory. They found their solution through the use of customized software applications and commercial of the shelf (COTS) hardware.
The VSIF is located in Fort Worth, Texas, and is used by Lockheed for the fusion of new hardware and software subsystems for the F-35. The facility features an F-35 spread out over a gymnasium-sized area, with a hardware-in-the-loop testbed that runs real code on real hardware, as well as a motion-based F-35 simulator.
The challenge encountered by Lockheed’s VSIF team was multifaceted, as they needed an integrated system capable of monitoring aircraft sub-system integration tests. This also required capabilities such as real-time display capabilities and the ability to manage all of the system components from transducer setup to data management.
Dave Baker, senior vice president of engineering and manufacturing and partner for G Systems, said it was able to meet Lockheed’s needs for the F-35 VSIF with a combination of high channel count data acquisition architecture and flexible configurable hardware. G Systems worked with another Texas-based automated test equipment provider, National Instruments, to solve the F-35 VSIF challenge.
“One of the main design challenges for the system was to build a large distributed platform using COTS equipment and software tools rather than proprietary black box solutions traditionally used. Since the system aggregates data from multiple sources, time synchronization was also a primary concern,” Baker told Avionics.
The data acquisition system architecture was established to be distributed across several servers that would help to enable load balancing and achieve the required system performance, according to a case study published on the project by G Systems.
Future expansion for the system was also achieved by G Systems developing six custom software applications within a distributed software architecture.
Ultimately, G Systems and NI produced a hardware system that “exceeds the initial requirements” prescribed by Lockheed Martin, Baker said. VSIF is using a system with a total of 45 data acquisition cards and a mixture of XI-6070E, PXI-6031E, PXI-6052E, and PXI-6534 distributed across five PXI chassis linked by fiber. Time synchronization for the system was achieved by using a Microsemi IRIG-B board and reflective memory was configured using hardware supplied by Curtiss-Wright.
The system delivers data to F-35 VSIF engineers in engineering units, accounting for calibration values for the various components of the system including the transducer and signal conditioning module.
Cost control around hardware used as part of the system was also a major concern for the project.
“By selecting COTS equipment, we were able to apply the best solution for each portion of the system. We provided several software applications that seamlessly communicate with a master system database for joining a variety of hardware together from several manufacturers for a cohesive user experience,” said Baker.
Baker said the system can be further customized to “fit a variety of cases.”