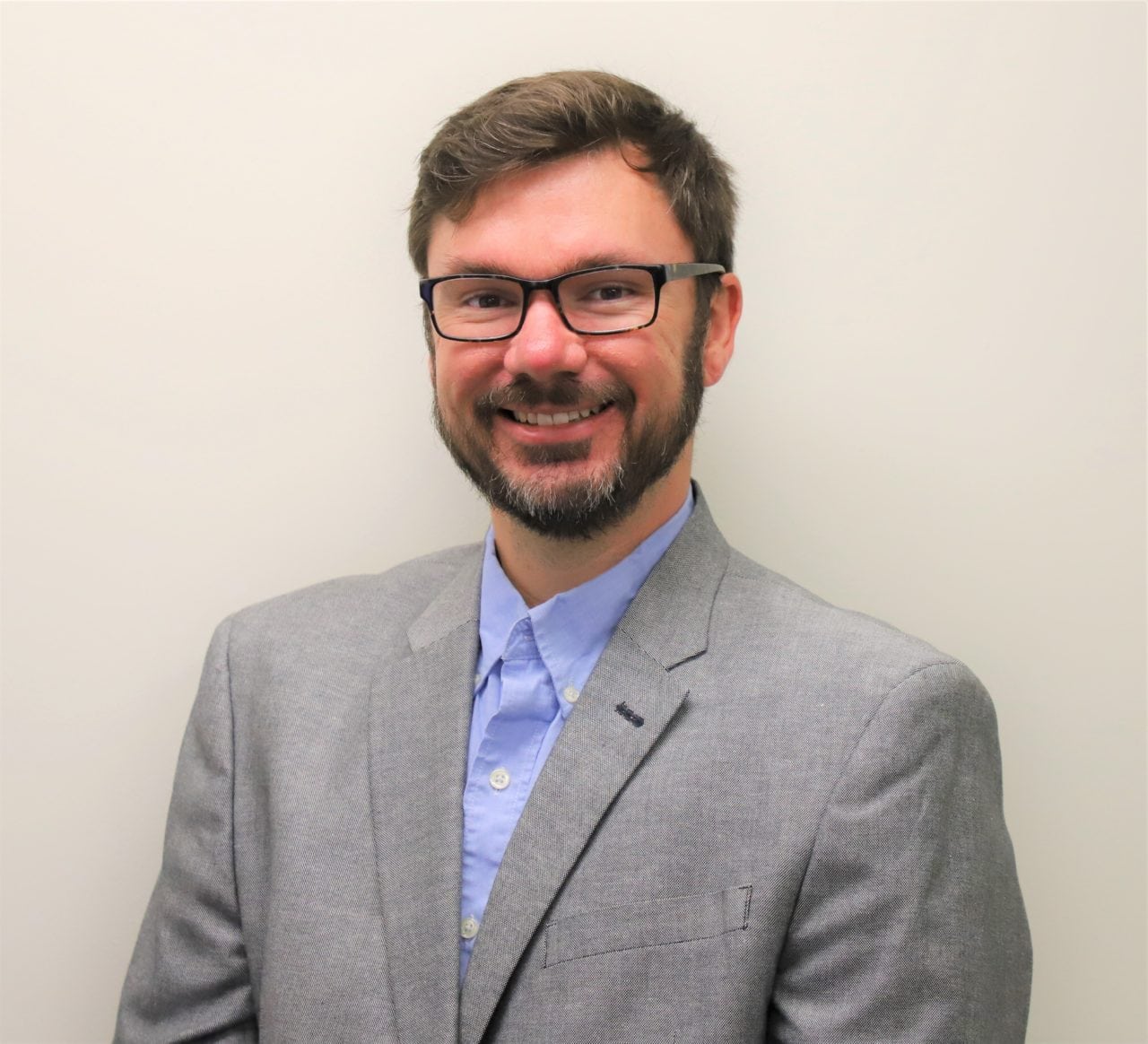
(Textron Systems)
Sean Baity spent his first wedding anniversary on a cross-country trip with his wife.
Also in the van with the celebrating husband and wife were three other guys and two 100-pound autonomous ground vehicles. Baity’s robotics team had been asked to show off their work at a conference in Salt Lake City, Utah, so they were driving there from Blacksburg, Virginia.
“We look back fondly on it,” he said.
That anecdote is typical of Baity’s passion for his work. The Maryland native earned a degree in mechanical engineering from Virginia Tech, then doubled up with a Master’s degree in the same field focusing on unmanned robotics. In the decade-plus since what must be the most romantic robotics convention in history, his focus has followed industry trends from the ground to unmanned aircraft systems (UAS).
Baity is now the technical director for advanced product initiatives for Textron Systems, parent company Textron’s unmanned-specialized subsidiary. He spoke to Avionics about his position and what he’s working on at Textron Systems.
Walk us through your day-to-day work at Textron Systems.
It’s evolved over the years. Originally, we were kind of doing these projects in the background. For instance, the boat that is now the unmanned deploy-and-sweep system for the U.S. Navy. We started that back in 2006, and it was myself and a couple interns over the summer, and we took on the job of going down to the harbor and running a boat. It’s evolved through that process to testing new field-flying and testing systems.
My current day to day — I go between a variety of projects across the business both here at Textron Systems as well as our Textron portfolio including Bell specialty vehicles and other folks in the business. It’s a much broader perspective, and I wouldn’t say there’s one project that keeps me busy.
Specifically, what do you do with those projects?
My role is bridging the gap between the program areas and business with the technical community. How can we adapt existing products to make them more aligned? One example there is quad technology. We had our president/CEO come in and say, “What’s next for the Aerosonde program?” We sat down and said, “This is what we think would provide a lot of value.”
Traditionally, unmanned systems are measured in how long they can fly; more endurance was the metric for pushing the limits of the market for a number of years. We decided to take a pretty capable, persistent endurance aircraft and sacrifice that for the ability to take off and recover vertically without the need for any sort of launch recovery equipment on the ground with the idea that there’s not an immediate contractual need, but our user community could use that in certain situations and perhaps would like to use it to develop new situations in which they can use unmanned aircraft system effectively.
Talk about the X5-55.
We really selected it around the idea of a scalable concept. We said, “Well, we’ve got to pick something to build and try” because that practical learning and the challenge of actually putting together something that flies informs quite a bit more than sitting down and doing paper studies is my view. So we picked something that would be consistent with our business that sits on the upper end of the smaller class of vehicles that were in Part 107.
We wanted to take on the challenge of maximizing that vehicle class while being able to provide this expeditious platform that doesn’t require extra ground-support equipment. You don’t need a launcher, you don’t need a net, you don’t need a parachute or those other trappings and look at it as a potential extension of our capability ecosystem, what we have for mission payloads for civil, commercial and defense applications that it could be used for.
The X5-55 is a relatively wild idea; it’s an airplane without traditional control services. It’s pretty easy to just say, “Well, put them on there,” and everybody gets warm and fuzzy with that. But we took on a challenge to say, “Yey, let’s not do that; let’s try it a different way and push the boundaries of what we’re comfortable doing and take those hard lessons and put in that hard work to generate what that experimental platform that testbed has yielded thus far.”

The X5-55 unveiled at AUVSI Xponential in May 2018.
What have you tested with the X5-55, and what has come of that testing?
What we have tested on it is the propulsion system. We have the airframe, and we built a propulsion testbed which allows us to look at how do we effectively distribute electric propulsion. There are a lot of multirotors out there, but we’re actuating them independently, so they’re vector-thrust on all four corners. How do we manage that? How do we mechanically integrate it, how do we electrically integrate it and, primarily, how do we control it effectively to provide the aircraft the ability to maneuver and do it in a durable and robust way? What happens when this failure mode occurs? What’s the corrective action? What’s the anticipated result? How does it degrade and then it also drove how we do business here? We do a lot of customer-oriented rapid development particularly in our Aerosonde program supporting our flight operations.
You mentioned that you spend your days on a lot of different projects. Is there anything you are working on right now that you can tell me about?
The X5-55 is one of the more exciting projects that we’re working on and the derivatives that come from that. I would say our efforts and the projects that are the most exciting to me are about how do we make unmanned aircraft systems more relevant to the future?
There’s this open question of what’s the future of unmanned aircraft — what does it look like? And in my view, it’s probably something that doesn’t just fly around at relatively low airspeed and provide video that someone sits and watches in a seat somewhere remotely. It is more aligned to a system that is more nimble, more agile both in how it gets deployed and flown and also provides a greater level of distillation of information. So rather than having this in-depth training behind flying an unmanned system, a very unique skill set it, it would be more like walking up to an airplane and it tells you what you need to know and you really don’t have to have much training behind it to go operate.
Looking backward, as someone who has been in the industry for over a decade, where have you seen the most change?
I think one example is just the accessibility to the fundamental enabling technology. When we started in this or when I got involved with it, everybody built their own autopilot, for instance. There wasn’t anybody out there that sold a component that did the job. And then there was a trend in the industry to outsource everything. And there were suppliers, and there was an industry base. And it blossomed over the past five to 10 years where it’s evolved to the point that you can go to a show and see a college team that has a little booth there that is flying a little multi-rotor. Then, in two to three years, it’s proliferated.
It’s interesting in that it’s driven by that interest and everybody getting involved and trying to make stuff work. But translating that to the value proposition to make it stick or grow at the rate that it really can: that’s the biggest challenge. The money trail is very clear, it’s defense-oriented — get people out of harm’s way, providing information, better situational awareness, extend the reach of that battlefield commander to get a job done. That’s a very clear value proposition.
There is money backing out of the civil market with really cool applications and potential there as well, but we’re on the front end of that maturation.
There has been a lot of talk about military leveraging the commercial space more and the challenges that entail. How much do you think those spaces can work together?
There is tremendous opportunity for us to gather. And they largely have done that in my short view the industry. I think that the pace of change within the commercial side, the government sees the ingenuity of those putting blood, sweat and tears in as informative and energizing for their view. They have big challenges to go tackle, and speed is an asset. Good ideas are even better if you can get it faster.
What I see as a challenge is aligning with the way that the U.S. Defense Department does business and supports and sustain those assets beyond just the technical requirements. It’s got to be ruggedized, painted a certain drab color. But you get the entire service and the acquisition and the operational communities around the idea of moving into a pace of industry. It is quite a shift in the way that they view and sustain and support it funding the way the government does business.
What are your thoughts on integrating drones into airspace?
It’s paramount. in terms of being airspace. I enjoy the luxury of flying through that managed national airspace system quite often. So, I appreciate it immensely. I can get from point A to point B without really worrying about anything. At the same time, I recognize the challenges: we’re now going to add a tremendous amount of complexity and the apprehension of how to, one, accommodate and then integrate all that diversity into a pretty well-established and effective and efficient system today; and, two, with that rate of change, it’s imperative that we do it deliberately.
There’s been some changes in the past few years particularly the section 333 morphing in and followed on by the small UAS rule part 107 — it’s really given a little bit of wiggle room for industry to continue to innovate and move forward. I do think that other areas around the globe have been more accommodating are more aggressive, but in the same light, they’re working on a different order of magnitude of complexity.
This interview was edited for length and clarity.