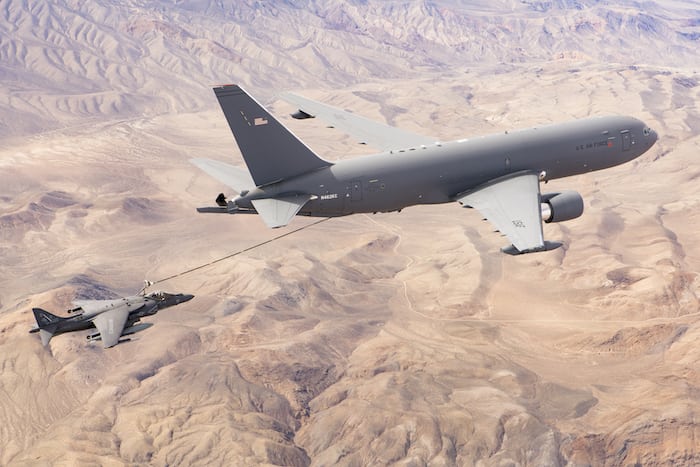
KC-46A completes a Milestone C flight test with an AV8B. Photo, courtesy of Boeing.
Boeing expects to deliver the first KC-46A to the U.S. Air Force in October. The aircraft has completed more than 3,300 flight testing hours and has cost the OEM billions to develop and certify. Here, Avionics provides a breakdown of the aircraft’s development costs a timeline for certification.
An overview of how its flight controls, boom operator station and avionics core networking configuration will provide a technological leap compared to the current generation of U.S. aerial refueling tankers.
First Delivery in October?
During Boeing’s second-quarter earnings call, the company’s executives explained how the OEM was charged $307 million related to cost growth of the KC-46A program associated with six flight tests and two “early bird” aircraft. According to Bloomberg, Boeing has accumulated $3 billion total in charges related to the development of the KC-46A.
“We continue to make steady progress towards final certification for the KC-46 tanker and recently completed all flight tests required to deliver the first aircraft, which is expected to be in October of this year, as now agreed upon with the U.S. Air Force,” said Boeing CEO Dennis Muilenburg, during the company’s second-quarter earnings call.
The Air Force is requesting $88.2 million to fund the ongoing KC-46 engineering and manufacturing post-production modification efforts. Another $2.9 billion has also been requested in procurement funding for low-rate initial production (LRIP) Lot 5 in January 2019. By 2028, the plan is to acquire a total of 179 new KC-46As.
Once the aircraft achieves certification, first delivery and entry into service, the U.S. Air Force pilots and boom operators will operate the next generation multi-role aerial refueling tanker well into the 2050s.
Here are some of the game-changing technologies being featured on the KC-46A.
Remote Vision System
KC-135 boom operators use specialized glasses to look through a window that shows the aircraft they’re attempting to refuel. Using a control stick, they insert the tube of the aircraft into the receiving aircraft. The head down display on the KC-135’s boom operator station also features steam gauge displays.
On the KC-46A, boom operators will use the aircraft’s remote vision system (RVS), which was adapted from the setup of a Boeing 787 cockpit. The RVS station has a large head down display, where the operator has push-button control over functions such as a traffic collision avoidance system computer and the boom itself.
The refueling station also has a graphics subsystem and can allow the boom operators to view both the physical fuel boom and refueling status data when performing a mission. The RVS station, positioned directly behind the cockpit, gives the operator access to a total of seven cameras, four of which are dedicated boom cameras, while the other three act as panoramic cameras. The cameras combine the use of 2D, 3D and stereoscopic technology.
In a 2011 edition of Horizons, an internal e-newsletter distributed to Rockwell Collins employees, Gladys Yanez, a systems engineer at the time, described the inspiration behind the use of stereoscopic technology as coming from a remotely controlled bomb disposal robot. The robot was in the company’s Cedar Rapids, Iowa’ factory dedicated to head down display development center (HDDC). It used stereoscopic 3D to complete missions, which also proved to be useful for the boom operator’s station.
The KC-30A, a modified Airbus A330 multi-role aerial refueling tanker, also features a remote vision system used by boom operators.
In May, when Boeing invited Avionics and several other publications to its factory in Seattle, Washington for a tour and overview of the tanker development program, the aircraft had completed 95% of its testing and was working through a software upgrade to help reduce boom scrapings, or unintended contact with receiver aircraft outside the refueling receptacle, according to Mike Gibbons, Boeing’s KC-46 vice president and program manager.
Now, the program has completed 100% of flight testing and awaits certification.
787 Cockpit

Boeing KC-46A tanker cockpit. Photo, courtesy of Rockwell Collins.
The KC-46A is a Boeing 767 with a 787 cockpit, which has the equivalent of four average-sized laptop screens in use as head-up displays along with two Class III electronic flight bags. Each of the displays on the KC-46A are multifunction displays and are split into two windows where pilots can independently display information such as airspeed, electronic checklists or system synoptics.
The overhead panel of the KC-46, like the 787, is configured with three control panels that feature satellite communications, VHF and HF communication functionality.
A difference between the KC-46A and a 787 is the aircraft’s tactical situational awareness system (TSAS) processor and display. Additionally, the KC-46 features Airborne E, which provides automated threat assessment and avoidance tasks for tanker crews, according to Rockwell Collins. KC-135 pilots must manually determine how to avoid terrain and surrounding traffic when they determine a reroute is needed in the event of an emergency. The KC-46’s TSAS automates this process.
Avionics Network and Future Upgrades
Under the cockpit and cabin of the KC-46A, are the computers that make up the aircraft’s signal data concentrator network, according to Rockwell Collins. The network is based on the ARINC 664 avionics full-duplex, switched-Ethernet (AFDX) standard. AFDX has been featured on the Airbus A380 and Boeing 787 as well as the Bombardier C Series. The use of deterministic ethernet provides a more flexible architecture for integration of mission systems and subsystems for the aircraft.
According to an ARINC 664 white paper published by Abaco Systems, a supplier of avionics networking and other embedded technologies and services, the AFDX architecture is configured so that each avionics subsystem, such as a flight control computer, has an embedded end system that acts as is interface with the AFDX interconnect. The AFDX interconnect interface uses a simple message interface to communicate with the aircraft’s various avionics subsystems, such as the flight management or air data computers.
Using ARINC 664 will help enable an easier path to future systems upgrades on the Air Force’s new refueling tanker.