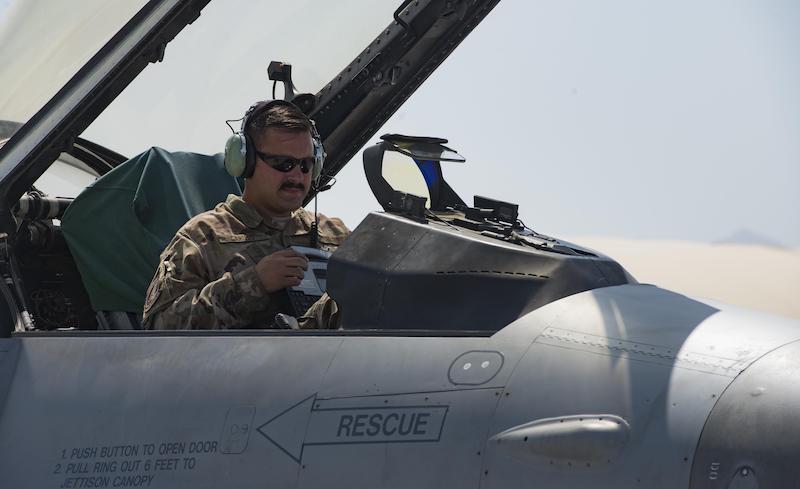
U.S. Air Force avionics technician Christopher Caruso conducting an operations check. (Air Force, by Benjamin Gonsier)
Aircraft maintenance, repair and overhaul (MRO) has progressed incredibly over the past 20 years. Maintenance is no longer just about turning wrenches because aircraft are incredibly complex and highly computerized.
Today, the U.S. Defense Department (DOD) recognizes that the right technologies will help it better understand how aviation systems are performing and gain predictive insights that optimize MRO readiness and the cost of sustainment.
Adm. Paul Grosklags, then-commander of Naval Air Systems Command (NAVAIR), reflected in 2017 that “One of our priorities … is to develop a more predictive capability for readiness. What we now need to do is become more predictive so that readiness issues never get to the point where we have to be sending ‘fire teams’ to deal with them.”
While innovative manufacturing and MRO practices have allowed military aircraft to become safer and far more capable, agencies are still facing critical adoption challenges. For example, efficient aircraft maintenance now requires MRO software, which recognizes and packages individual tasks where they fit best according to scheduling parameters (operational, revenue, maintenance, etc.). This means detailed visibility of individual components and their maintenance requirements are crucial for MRO practices to work correctly. But most machine data is not viewed. Most data viewed today is predominately for anomaly detection and control, not optimization and prediction, which provide far greater business outcomes.
In order to use internet of things (IoT) system data (i.e. machine data) to deliver enhanced visibility and efficient maintenance packaging, the DOD needs to make sure devices and sensors are reliably connected, secured and managed, and then the data is programmatically moved, computed and controlled.
Connecting, Securing and Extracting Data
Machines used in manufacturing or MRO for aviation have many different protocols for their communication and data. Extraction of this critical data can require a gateway, in this case, an IoT Gateway, to aggregate the sensor data, translate the protocols and process the sensor data before forwarding for extraction. The gateway performs several critical functions such as connectivity, protocol translation, data filtering and processing, etc. Gateways can also serve as a computing platform and enable edge or fog computing right where maintenance is performed.
Because manufacturing and MRO data can be very sensitive, the data needs to stay secure as it is extracted and moved. Technical specifications for a part to be manufactured by a computer numerical control (CNC) machine or additive manufacturing machine must be protected to prevent loss of intellectual property or data corruption, which could lead to improper manufacturing of parts causing operational interruption, equipment damage or even loss of life. Encrypted IPSEC tunnels between gateways, data centers and cloud(s) should be used to help protect data. Also, virtual private networks (VPN) and port forwarding should be used to enable secure remote access to devices behind the gateway.
Controlling and Computing
Once data is extracted and secured, the next step is to programmatically move and control that data. It should be simple — get the right data to the right processes and people at the right time to drive improved mission outcomes.
However, it’s not that simple. IoT machines and devices are very diverse and represent numerous manufacturers, purpose, age, etc., and can be geographically distributed at numerous sites. So data control policies are needed to ensure that the right machine data is unlocked, securely moved to the right applications and finally accessed by only the right people as needed. For example, continuous extraction and monitoring of a milling machine’s vibration levels, electric consumption and other variables will allow depot MRO operators to avoid unplanned downtime by identifying and responding to early indicators of impending failure. Advanced machine learning software can consume the extracted machine data and identify trends indicating impending failure that can interrupt or shut-down critical MRO production.
Additionally, event processing at the edge, or in the cloud, will enable data policy rules to execute on data in real time or near-real time, driving data movement related to operational measurements. For example, machine data may be transmitted once every minute when internal pressure is below a given threshold. If that threshold is exceeded, the machine data may be transmitted every few seconds. If the temperature exceeds a secondary threshold or increases at a specific rate over multiple observations, the data may trigger a specific action. That action could be alerting an operator or it could be initiating a graceful shutdown of the machine to prevent catastrophic damage.
There is no doubt that defense agencies can further utilize data to transform maintenance and aircraft MRO. In fiscal year 2016, the DOD spent $35.2 billion maintaining 13,935 aircraft, just a portion of the overall maintenance requirement when vehicles and ships are considered. Matching continually improving processes with advanced information technology will unlock a massive amount of machine data available in operational systems and maintenance facilities, leading to significantly improved readiness through optimal utilization of limited maintenance facilities and personnel to drive increased MRO production and efficiency, as well as deliver cost savings.
For the DOD, truly digitizing operations means maximizing the potential insights from MRO machine data. It will enable better decisions, improve allocation of resources and ultimately drive mission readiness and success.
Joe Beel serves as a defense industry strategist for Cisco Systems. He retired from the U.S. Navy as a captain, having served as a helicopter pilot flying from frigates and cruisers and as an acquisition professional.