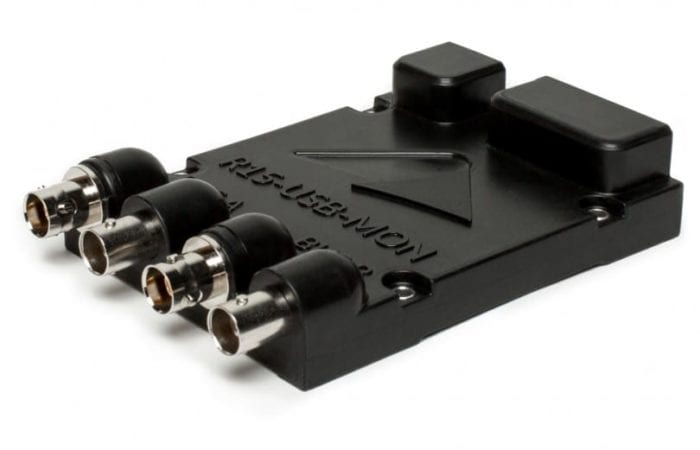
The BT3-USB-MON. Photo courtesy of Abaco Systems
Abaco Systems has unveiled a new hardware and software bundle capable of performing the type of MIL-STD-1553 data bus visualization, analysis and recording that normally requires three different data bus-testing technologies.
The MIL-STD-1553 serial data bus was first established in 1973 by the Society of Automotive Engineers (SAE), with initial deployment on U.S. Air Force F-16s before going on to be the most widely used bus protocol in military air and land vehicles. Over time it has moved well beyond the military realm. Today it is being used in some of the newest in-service commercial aircraft such as the Airbus A350, which uses a 1553 bus in its rudder control system and other safety critical systems not running on the aircraft’s avionics full-duplex ethernet (AFDX) architecture.
However, while 1553 remains a viable standard, it requires in-depth knowledge to be tested and debugged, according to Joshua Jensen, an avionics product manager at Abaco. Newer engineers are more familiar with more modern protocols such as ARINC 664 — the official nomenclature for the aforementioned AFDX network.
The increasing use of field-programmable gate arrays (FPGAs) in testers also helps to reduce equipment size, weight and power as well as to increase its versatility and upgradability. Portability and convenience also account for the popularity of universal serial bus (USB)-linked testers. Ethernet is also expanding in its applicability as a medium data bus testing.
Jensen said there were a number of factors influencing Abaco to introduce its new BT3-USB-MON 1553 data bus testing system.
“Although the MIL-STD-1553 and MIL-STD-1760 specifications are quite mature, we have seen many differing interpretations and/or violations of the specifications built into numerous avionics systems, including excessive response times, signals with insufficient amplitude and busy bit response on power-up occurring too late. Engineers performing upgrades to legacy systems often have little experience with these bus standards — yet need affordable and easy to use tools that provide a clear representation of bus traffic,” said Jensen.
The BT3-USB-MON is compatible with any 1553-compliant components within 1553 architecture. The system is capable for providing run-time 1553 traffic analysis and monitoring, bus recording and has a graphical user interface that gives a view of what is happening within the bus.
Abaco’s engineering team also focused on reducing the need for newer engineers to acquire extensive 1553 knowledge by adding software to the system that can capture anomalies within bus traffic by setting triggers.
A 1553 bus architecture is capable of up to 32 remote terminals or nodes within aircraft systems. One challenge this can present to engineers is attempting to conduct electrical analysis from cables that are difficult to access. Jensen said Abaco has even seen engineers attempt to create what he describes as “T” couplers using paper clips or stripping cables bare to expose a differential pair and analyze traffic on two different channels.
“It may be inserted anywhere in the bus topology,” said Jensen. “This tool can be deployed anywhere 1553 bus monitoring/recording is required, but it’s specifically targeted to give the engineer an intuitive GUI bus analyzer and logger capable of monitoring 100% bus duty cycle in a rugged, portable, low current consumption.”