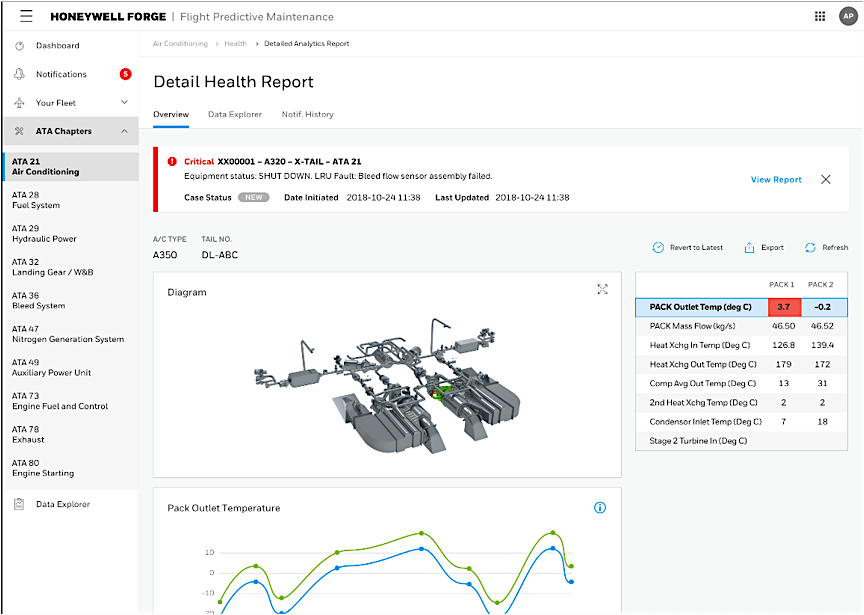
Honeywell’s FORGE analytics platform was developed to provide actionable insights to the various segments of an airline. Photo: Honeywell Aerospace
Launched in June, the Honeywell Forge data analytics tool allows airlines to save up to $200,000 per aircraft per year in fuel costs and up to $40,000 per aircraft per year in maintenance costs, Honeywell executives said in a Nov. 14 Avionics International industry webinar, “The Connected Aircraft: Creating a Node for Maximum Optimization.”
Honeywell Forge is a technology stack capable of collecting, cleaning and analyzing wide swaths of data from a variety of airline sources for predictive analytics. The integrated software solution combines a range of individual aircraft and overall airline data into a dashboard that airlines can customize.
In service with more than 100 airlines globally, the tool has already had results, including a 30 percent reduction in delays and cancellations at Cathay Pacific, according to Honeywell.
Honeywell can pair the advanced data analytics platform with its aircraft data gateway box, first introduced in 2017, as a method for wirelessly transferring data on and off of aircraft, though Forge works with any available quick access recorder or edge processing onboard system, the company said.
“We believe we’re pushing the envelope in taking safety, data, security, analytics and, ultimately, airline efficiency and productivity to a whole new level with Forge,” John Peterson, vice president and general manager of software and services at Honeywell Connected Enterprise, said during the webinar.
 | Want to hear more on aircraft connectivity applications? Check out the Global Connected Aircraft Podcast, where Avionics editor-in-chief Woodrow Bellamy III interviews airlines and industry influencers on how they’re applying connectivity solutions. |
For airlines, the hundreds of thousands of dollars in savings per aircraft per year “is a significant amount of money because this is profit,” Peterson said. “We call it packets to profit. You take packets of data, and you turn it into dollars of profit.”
In offering Honeywell Forge, Honeywell is able to take advantage of its “large install base,” which includes 25,000 engines, 20,000 braking systems, 30,000 APUs, 20,000 flight management systems, 300 services and apps, 10,000 satcom terminals, and more than 1,800 aircraft with JetWave, according to the company.
“We took a look and talked to the airlines, and we see that there are over $25 billion lost in flight delays,” Peterson said. “There’s $10,000 per hour [spent] on grounded aircraft due to unforeseen situations.”
In designing Forge, Honeywell saw an opportunity to reduce “the amount of waste in terms of delays, cancellations and groundings,” he said.
Forge offers an in-depth look at aircraft statistics to show airlines what is going well and what issues need addressing.
The system offers benefits in passenger experience, flight operations, ramp operations and fleet operations, including faster Wi-Fi speeds with global coverage, a five percent savings in flight times with Air Traffic Control priority, an improvement in arrival times and dispatch speeds, an up to 25 percent reduction in troubleshooting time on the ramp and reductions in aircraft turnaround times, and a reduction in operational disruptions by up to 35 percent, according to Honeywell.
Using satellite communications over L-band, Ka-band, or Ku-band, Forge is “like Waze in the sky” to allow the most efficient and safest flight path, Peterson said.
Through satcom and new, secure flight data recorders, Honeywell Forge also enables real-time safety alerts through its Black Box in the Sky (BBITS), which streams data to identify when aircraft enter hazardous flight conditions and to allow Airlines Operations Centers (AOCs) to advise corrective actions/emergency procedures and to inform Air Traffic Control centers of flight plan changes to reduce pilot workload.
One Forge dashboard element–lateral profile view–depicts flight paths and holding patterns around airports worldwide and can provide insights to airlines on available runway shortcuts that the airlines can present to air service navigation providers.
“We’ve had airlines like Etihad [Airways] and Lufthansa, who are customers of ours, generate tremendous efficiencies by using lateral analysis,” Julie Vasquez, flight efficiency leader for Honeywell Connected Enterprise, said during the webinar.