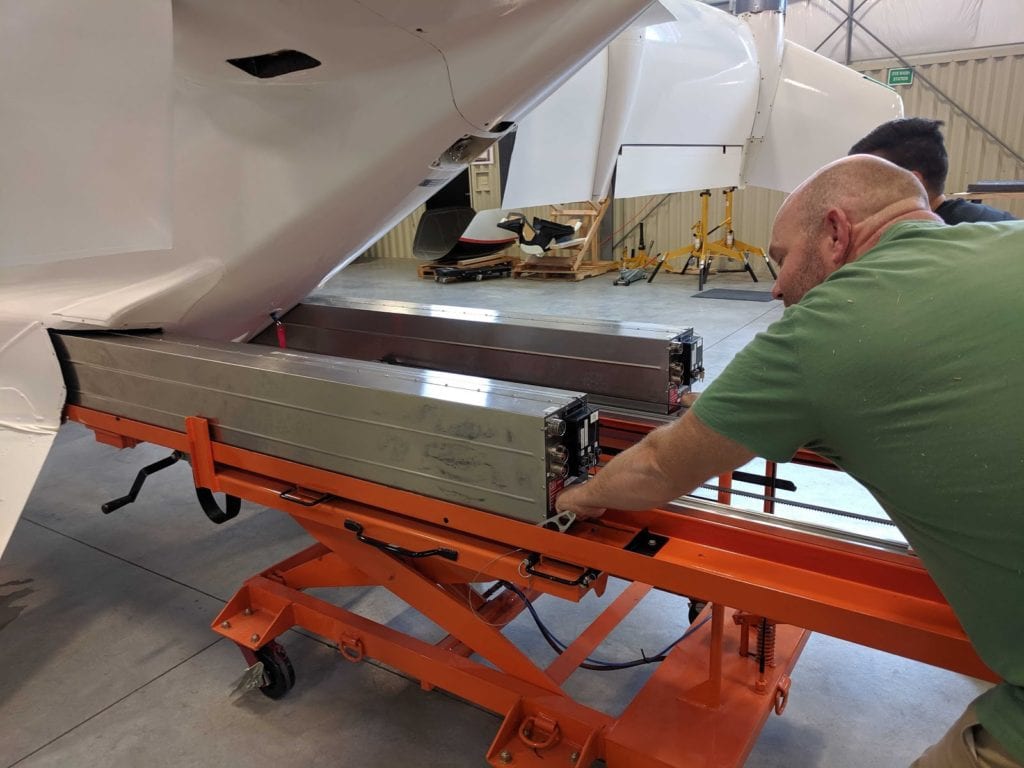
Air taxi developers face difficulties obtaining the proper battery packs at reasonable prices. Airbus’ Vahana project used two 300-pound lithium ion batteries, custom-made by Airbus Defense & Space. (Airbus)
SAN JOSE, Calif. — Designers and manufacturers of electric air taxis may run into issues sourcing the batteries they want at reasonable prices, according to a presentation given by Robert Hess, systems engineering manager at BAE Systems, at the Transformative Vertical Flight 2020 conference hosted by the Vertical Flight Society.
While significant advancements continue to be made in lithium-ion battery power, storage density and cycle life, battery cells ideal for electric cars and most other common applications don’t match the usage profile of electric vertical takeoff and landing (eVTOL) aircraft, Hess explained to Avionics International.
“An automotive battery, particularly if we look at a passenger car, is a vehicle that’s only operating maybe an hour, an hour and a half a day,” Hess said. “The biggest issue car operators have is range anxiety … aerospace wants a very high power and lots of utilization, and passenger cars really look for much lower power levels and much lower utilization.”
Battery cell chemistry involves tradeoffs between specific power — the amount of power the cell can exert at once — and energy storage density, as well as cycle life. The ideal chemistry for passenger cars is therefore very different from eVTOLs, which require high levels of power to get off the ground and maintain control in ‘helicopter’ mode. Since air taxis intend to reach profitability by maximizing utilization, cycle life is also critical to aircraft manufacturers.

A ‘Ragone plot’ demonstrates the specific power versus storage capacity of various battery cell compositions. (V. Srinivasan)
As a result, eVTOL companies — which, at this stage, don’t seek production at a scale that commands authority — are likely to face difficulties and drastically higher prices than automakers when searching for battery suppliers.
“As an industry trend, when we take a look at where battery production is going, of course the battery manufacturers are trying to sell their product into the largest, most viable market space,” Hess said. “When you look at current electric vehicle applications, it’s automotive that is driving a lot of demand for product … when we contrast that to aerospace, right now we are in the very early stages of defining demand and understanding what we need to do here.”
Automakers look to procure battery packs for between $100-150 per kilowatt-hour (kWh), according to Hess, but that price point is currently unattainable for aerospace.
 | Want more eVTOL and air taxi news? Sign up for our brand new e-letter, “The Skyport,” where every other week you’ll find the most important analysis and insider scoops from the urban air mobility world. |
“Uber has numbers they put out in some of the Elevate work in terms of where they think they need to fit … If you’re doing a low-volume production pack or a demonstration pack, it’s not going to be $150 a kWh. It’s not going to be $250 a kWh. It’s not going to be $500 per kWh,” Hess told eVTOL aircraft developers. “You could [pay] $1,000 a kWh, and if you’re using an esoteric chemistry that’s being hand-built by people someplace in some factory, it could be $20,000 a kWh. These are real numbers of what you might expect to see.”
Uber, which is attempting to create affordable air taxi networks through its Elevate project and vehicle partners, declined to share specific figures regarding battery pack pricing targets, but agreed that “a stable and reliable supply of high-quality cells and battery packs as paramount to the success of Uber Air and electric aviation generally.”
“Uber Elevate is building relationships with top cell suppliers and is investing in development and validation of battery pack technology tailored for aviation applications,” said Luke Wilhelm, Uber’s head of vehicle engineering. “We do not intend to manufacture battery packs, but consider the development of the technology and supply chain as necessary for the success of Uber Air.”
There is one current application of electric batteries that closely matches what eVTOL aircraft are likely to need: electric transit vehicles, such as buses, which often operate for ten or more hours per day. BAE Systems is a supplier of battery management and electric propulsion systems for electric transit fleets — part of the company’s background that informs its move into aircraft electrification and eVTOLs.
The stringent certification requirements of aerospace create barriers to entry as well, not only for initial product manufacturing approval, but also preventing battery manufacturers from tweaking or upgrading product lines as rapidly as they would for cars or other uses.
“Certification takes a long time and it’s quite expensive for all the rigor we want to have to make safe, reliable aircraft,” Hess explained. “We can’t just allow changes to be made, even in the supply base. Aerospace drives a much more rigorous and controlled process of the supply base. It’s not that the [automotive] supply base doesn’t do a very good job — it’s phenomenally good at providing high-quality products, but at a very different timescale. As a simple example, new processors come out every year, but we don’t upgrade our flight control computers and so forth every year with a new processor.”
For automotive and other common applications, battery suppliers may maintain a product line for 18 months, Hess said; aerospace applications would likely require a battery pack — and its individual cells — to be produced as certified for 5-7 years, or even longer.
“Our demand is miniscule, and so we just do not have the buying power to get access to those products in terms of volume and an acceptable price point,” Hess said. “I think in the short term, the industry is going to have to make its own batteries.”
Jeff Engler, CEO of Wright Electric — a startup targeting 2030 for the introduction of a 186-seat all-electric commercial jet — agreed that the emerging electric aviation market faces sourcing concerns related to batteries.
“The requirements on the ground and in non-aerospace applications are very different from those at 35,000 feet,” Engler told Avionics. “Across the supplier chain, from batteries to motors and inverters, there are not a lot of people doing this, and so you really have to pick your suppliers well and understand that if you want to get into this space you ultimately have to become more vertically integrated than if you’re in a more mature industry.”