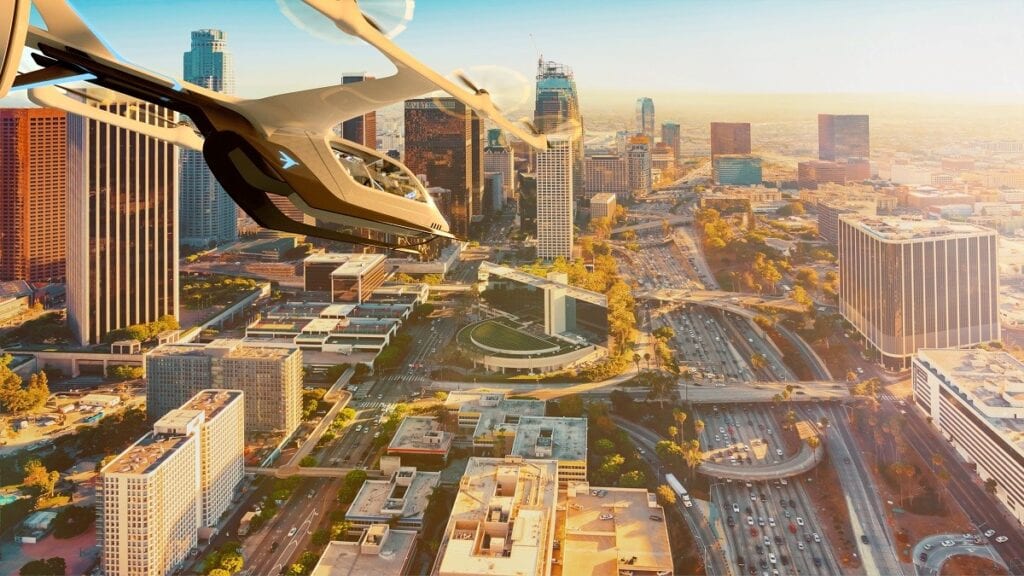
An interview with Cuberg founder Dr. Richard Wang sheds light on the battery challenges and solutions driving dynamics in the electric aviation revolution. (Image: Embraer)
It’s no secret that improvements in battery characteristics will define the possible applications and time-to-market of both fixed- and VTOL electric aircraft.
Trainers (Pipistrel’s Velis Ectro, Bye Aerospace’s eFlyers) and some small retrofitted aircraft have been successfully demonstrated using today’s batteries, with around 250-270 Watt-hours per kilogram (Wh/kg) of specific energy. Many industry leaders suggest an energy density around 350 or 400 Wh/kg is necessary for the industry to really emerge.
Dr. Richard Wang, who founded Cuberg in 2015 to pursue research and commercialization of lithium metal batteries, told Aviation Today the capability of lithium-ion cells — the dominant cell chemistry used in consumer electronics, electric cars and now for most electric aircraft projects — is plateauing, with power density no longer seeing a steady five percent annual improvement.
Cuberg has raised $10 million in funding from Boeing HorizonX Ventures, the U.S. Army, the California Energy Commission, the U.S. Department of Energy, the National Science Foundation and CalSEED.
In June, an independent analysis of Cuberg’s lithium metal pouch cells conducted by the Idaho National Laboratory indicated a specific energy of 369 Wh/kg, specific power of 2,000 W/kg, and a 370-cycle lifespan, calculated as when the battery drops to 80 percent of its original capacity.
While that cycle life isn’t yet sufficient for use by high-utilization aircraft, Wang told Aviation Today his team expects within the year to achieve a cycle life of 500 — which is where potential customers tell him the product becomes very attractive — and exceed a cycle life of 1,000 within two to three years. Wang also expects the cells to meet all the requirements for aerospace-grade certification within the year, though the formal process will take longer than that.
“We’re actively working with many or even most of the leading electric aviation players,” Wang said. “And we’ve gone through sample qualification with a few of the most prominent ones … our cell is one of if not the only cell that has met the full suite of their performance wishes.”
Cuberg is also working with a number of drone companies as well, especially on the larger end of the cargo delivery space.
“Cargo-driven applications are going to be relatively early in terms of adoption,” Wang speculated. “The other most promising area is these small, two-seater and four-seater retrofitted fixed-wing aircraft, using an existing airframe and swapping out the propulsion system. We see those customer segments picking up very quickly, and then the Uber Elevate air taxi model is more ambitious and will take a little longer to build out the full ecosystem.”
There are a few other battery chemistries being researched as alternatives to Li-Ion that will allow electric vehicles to move beyond their plateauing capacity. Oxis Energy and Texas Aircraft recently announced a partnership to electrify the light sport Colt S-LSA using the former’s lithium-sulfur (Li-S) batteries, expecting an energy density of 400 Wh/kg, but at the price of between 200-300 cycle life performance, according to the companies. Additionally, Li-S battery packs are often much larger than Li-Ion alternatives, according to Dr. Wang, even if lighter — and cargo aircraft often max out available volume before weight.
Tesla and SpaceX founder Elon Musk has opined that 400 Wh/kg of energy density with high cycle life, produced in volume, is necessary for electric aviation applications — a benchmark he recently tweeted is “not far. Probably 3 to 4 years.”
Wang, who interned at Tesla’s Cell Research Lab while earning his Ph.D. at Stanford University, agreed with Musk’s characterization and speculated the company is working to move past the limitations of Li-Ion batteries through either silicon anode technology or lithium-metal applications similar to Cuberg.
“We have some strong suspicion that Tesla is working on silicon anode technology, and that is one potential way to get there, although the technology still needs some R&D and process breakthroughs to be commercialized,” Wang said. “They have a well-publicized partnership with a renowned Canadian battery lab that is working on some lithium-metal approaches as well.”
The lithium-metal approach has two advantages, according to Cuberg’s founder. In addition to being fully compatibility with most manufacturing processes used for Li-Ion, which will make production at scale much easier than alternatives, Cuberg’s cells use a non-flammable proprietary electrolyte that significantly reduces the risk of an electric fire, as experienced by Eviation’s Alice prototype in January. If safer cells are developed and validated, then battery packs using those cells can be safely designed with less extra cost and weight compared to conventional Li-ion, according to Wang.
Currently, many electric aircraft companies are either using B- and C-grade automotive cells — the higher-quality cells typically go to volume customers — or cells procured from Chinese suppliers. Neither of these options offers the safety and rigor throughout the supply chain necessary for aerospace-grade certification, according to Wang.
Cuberg intends to keep its focus on supplying cells rather than designing battery packs, but is currently forming partnerships to produce a common reference model (CRM) for an efficient pack — similar to the aircraft eCRMs released by Uber to assist eVTOL manufacturers in the process of designing an all-new class of aircraft.
Currently, the startup is shipping a few hundred cells per month to top engineering teams within the sector, and intends to ramp up this year to a few thousand cells per month. The company is building out an expansion that “should take us to 10-30,000 cells per month,” according to Wang, with the average prototype using 5,000-10,000 cells. After that, greater scale will be pursued based on customer demand and market evolution.
Of course, Cuberg isn’t the only startup pursuing commercialization of lithium-metal batteries. Quantumscape, a battery startup counting Volkswagen, Bill Gates and a number of venture capital firms among its investors, merged with Kensington Capital through a $3.3 billion SPAC deal this week to go public on the New York Stock Exchange. Quantumscape told the Financial Times it aims to produce enough batteries annually by 2028 for 910,000 electric vehicles.
Cuberg intends to compete in that market, too, but sees the emerging electric aviation market as an ideal stepping stone.
“We see aviation as a very good early application, but ultimately the automotive industry — electric vehicles — is going to be the largest market for us for the foreseeable future,” Wang said. “So we have built up some very strong relationships with key players, looking at three plus years out.”