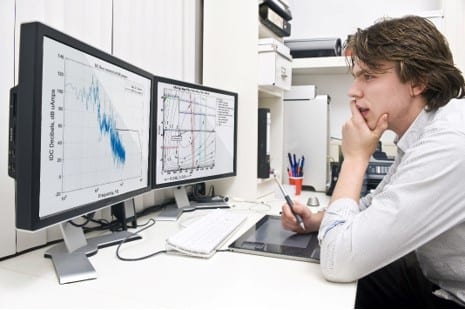
LaunchPoint says that MAAP will help eVTOL companies avoid costly design mistakes by showing engineers what a vehicle’s powertrain looks like before a prototype is built. The tool will work for aircraft with varying power levels, rotors, battery and fuel levels, and overall system layouts. (LaunchPoint)
The design tool which allowed LaunchPoint Electric Propulsion Solutions, Inc. to develop its patented electric motors and hybrid-electric propulsion systems is now available for commercial use, the company announced. Modeling Advanced Aircraft Propulsion (MAAP) is described by LaunchPoint as a tool for better developing emerging electric vertical takeoff and landing (eVTOL) technology.
“The propulsion system, so that would be the batteries, the controller, and the motor, is the most novel of the advanced technologies in the eVTOL,” Rob McDonald, former aircraft design lead at Uber Elevate, industry expert, and LaunchPoint advisory board member, told Aviation Today. “That’s the subsystem, that’s the set of parts that aircraft designers have the least experience with.”
LaunchPoint says that MAAP will help eVTOL companies avoid costly design mistakes by showing engineers what a vehicle’s powertrain looks like before a prototype is built. The tool will work for aircraft with varying power levels, rotors, battery and fuel levels, and overall system layouts.
“LaunchPoint is uniquely positioned to work with air vehicle integrators to help design aircraft propulsion systems and to validate designs for the Advanced Air Mobility market,” Rob Reali, LaunchPoint’s CEO, said in a press statement. “In addition to the MAAP design tool, we also provide a suite of electric motors, controllers, and generator sets that are ideal in certain classes of vehicles this exciting industry is developing.”
McDonald said MAAP is a conceptual design tool for electric motors that run on primary inputs. The primary inputs give the tool specifications to model the motor from.

LaunchPoint’s “propulsion-by-wire” is a next generation concept for eVTOLs that borrows from the well-known fly-by-wire concept featured in most modern commercial and business aircraft. (LaunchPoint)
“The primary inputs are the design points you need to design around,” McDonald said. “So, for a motor, that’ll be, typically, the torque and speed of the different loads that you need. And there can be multiple design points that correspond to different points in the mission. For example, you’ll have a certain torque and speed requirement during takeoff, a different torque and speed during cruise, and a different torque and speed, say during an emergency situation. So you have multiple design points that you can input.”
MAAP also allows users to control other secondary and tertiary inputs like altitude, temperature, ambient conditions, and material properties, McDonald said.
“There are certain constraints that are that are inherent,” McDonald said. “You don’t want it to break, you don’t want it to overheat, and things like that, but then there’s certain constraints that the user has control over. Things like maybe your application has a maximum diameter of the motor, then you can put in that maximum diameter. You might have a minimum efficiency requirement and something like a minimum installation life.”
From these inputs, MAAP will give the user system performance outputs like current and voltage levels at key system nodes, internal and external temperature, power loss breakdown identifying sources of heat and inefficiency, component and system efficiency, and proximity to all operational constraints. The tool will also provide the user with system mass including the breakdown to constituent parts, system and component dimensions, and a virtual specification sheet.
“Then the way it works is you run it, it’s an optimization-based design tool, and the normal optimization objective is to minimize the weight of the system, but there are some other objectives you can do for example to maximize the efficiency or other objectives you might want to use,” McDonald said.
Weight is an important consideration for all aircraft but especially for eVTOLs whose design often includes the use of heavy batteries.
“When you are developing a vehicle you either have to work with an off the shelf component or you have to work with a supplier to develop a product for you and eVTOL aircraft are revealing that off the shelf components don’t typically have the performance required to make each vehicle work,” McDonald said. “These vehicles really need a bespoke solution that works tailored with the design of the vehicle. And so, what MAAP does is it allows a company developing a vehicle that bespoke propulsion system designed to unlock that weight so they can put feasibility into their vehicle. It really helps achieve the performance that’s required to make eVTOL work.”
LaunchPoint used MAAP while developing the 6 KW hybrid-electric genset for drones and the 40 KW genset for larger drone cargo and air taxis.
“LaunchPoint has been using this kind of tool before you know before they decided to make it a product and make it available to others,” McDonald said. “They’ve been using this kind of optimization-driven conceptual design tool in house for a long time…They’ve used this kind of optimization-based design process to design electric machines from the customers’ requirements that are required to develop an optimal design that meets those requirements.”