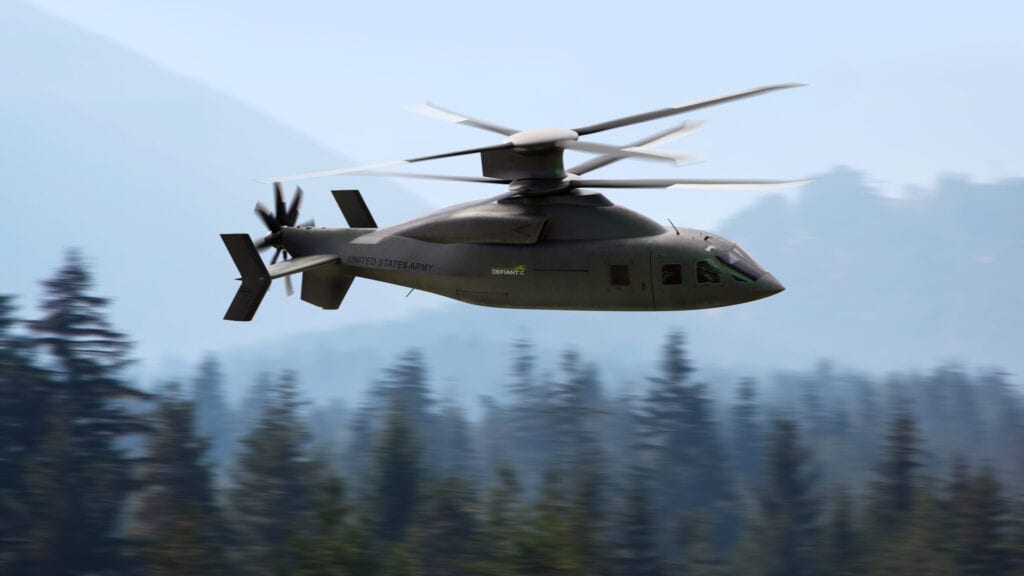
Sikorsky-Boeing’s Defiant X uses Sikorsky’s digital engineering expertise in its development.
The next generation of helicopters will include technology like autonomy and sophisticated fly-by-wire systems. To get there, helicopter original equipment manufacturer (OEM) executives are focused on digitization for the advancement of future helicopter design, manufacturing, and sustainment, panelists said during the Vertical Flight Society’s Forum 77 on May 10.
Digitization within the helicopter industry is not siloed within one area of the business. Executives expressed intentions to digitize multiple segments of their operations from design to sustainment.
“Digital engineering, digital manufacturing, and sustainment are critical to our business,” Paul Lemmo, president of Sikorsky at Lockheed Martin, said during the panel.
Sikorsky’s CH-53K and its combat rescue helicopter platforms were “born digital,” Lemmo said.
“I’m going to talk a little bit about the digital thread as well,” Lemmo said. “That’s a big part of where Sikorsky is headed, and it’s really where we are today. It’s not just a vision for the future, we’re actually living it today.”
Lemmo said Sikorsky digitally transformed its workforce to adapt to these new technologies for the CH-53K and combat rescue helicopter programs.

The Sikorsky CH-53K helicopter achieves a 36,000-pound lift for the first time at Sikorsky Development Flight Center in West Palm Beach, Florida, on Feb. 10, 2018. (PRNewsfoto/Lockheed Martin)
“Some of the things we’re seeing include the rapid acceleration of learning curves,” Lemmo said. “We’re experiencing the learning curve at unit 20 that we would normally experience at unit 100. So, these technologies really are proving themselves, and this digital thread is built into our current programs and used across our digital advanced manufacturing facilities at Sikorsky. The proven holistic lifecycle approach runs seamlessly throughout our design, development production supply chain and sustainment process.”
Mark Cherry, vice president and general manager at Boeing Vertical Lift, said Boeing is aiming to be the most digitally advanced company producing defense products.
“The most digitally advanced from an engineering standpoint easily produced is something that we see is revolutionary and foundational in almost everything that you see from eVTOL [electric vertical take-off and landing] to advanced propulsion systems,” Cherry said. “All that has to do with having a foundational digital trend.”
The future of the digital thread in helicopter capabilities at Boeing could include rapid capability updates during missions, Cherry said. The helicopter would be able to change its capability with adaptable software on route based on sensor information. They are also looking to use machine learning to decrease helicopter downtime between missions.
“If you think about the digital thread and really where it could go in the future, think about the back of a connected battlefield, the ability to have real-time updates, upgrades that are fielded extremely fast, software configurable mission systems, smaller and more frequent lots from a production standpoint, that allows for next generations and iterations to be done very quickly in terms of getting information back to the plant,” Cherry said. “So, you don’t have big monument tooling and in fixtures and things like that. Those are some of the big opportunities that we see for cost savings.”
Bell is aiming to use its digital thread to combine the expertise of its new technology and business processes, Glenn Isbell, vice president of rapid prototyping and manufacturing innovation at Bell, said. This will allow Bell to use new technology more efficiently and simplify its design systems.
“One of the things that we’re really applying is our digital design and our manufacturing thread to where we can really achieve the deep digital threading and connect those two pieces together as well as including our maintenance and sustainment costs,” Isbell said. “So, we can improve our program affordability and our aircraft performance. We realize that the way the world flies these products is going to be different in the future, and we plan to lead the way.”

The Bell 525 Relentless is working on a few remaining certifications for this aircraft which it expects to be finished by the end of this year.
Isbell says this work has already begun with Bell’s 525 Relentless helicopter. The 525 helicopter will be a commercial fly-by-wire helicopter. Bell is working on a few remaining certifications for this aircraft which it expects to be finished by the end of this year.
“This is going to be a revolutionary aircraft that’s going to have step function change in operating cost, efficiencies, and seat per mile,” Isbell said. “It’s really been designed with maintainer in mind.”
The digital thread also allows Bell factories to be connected and share data, Isbell said. This allows for the digital thread to start at the “birth” of a part all the way to the sustainment and retirement of that part.
“It is not our intent to make these next-gen vehicles…in the same way that we’ve made the existing aircraft that we produce today,” Isbell said. “There’s ways to keep the high aerospace quality but do those in a much more efficient way and this facility is our proving ground where we’re able to both understand those technologies and prove to the world that aircraft manufacturing can be done differently at step-function changes in capability that everybody kind of assumes is there.”