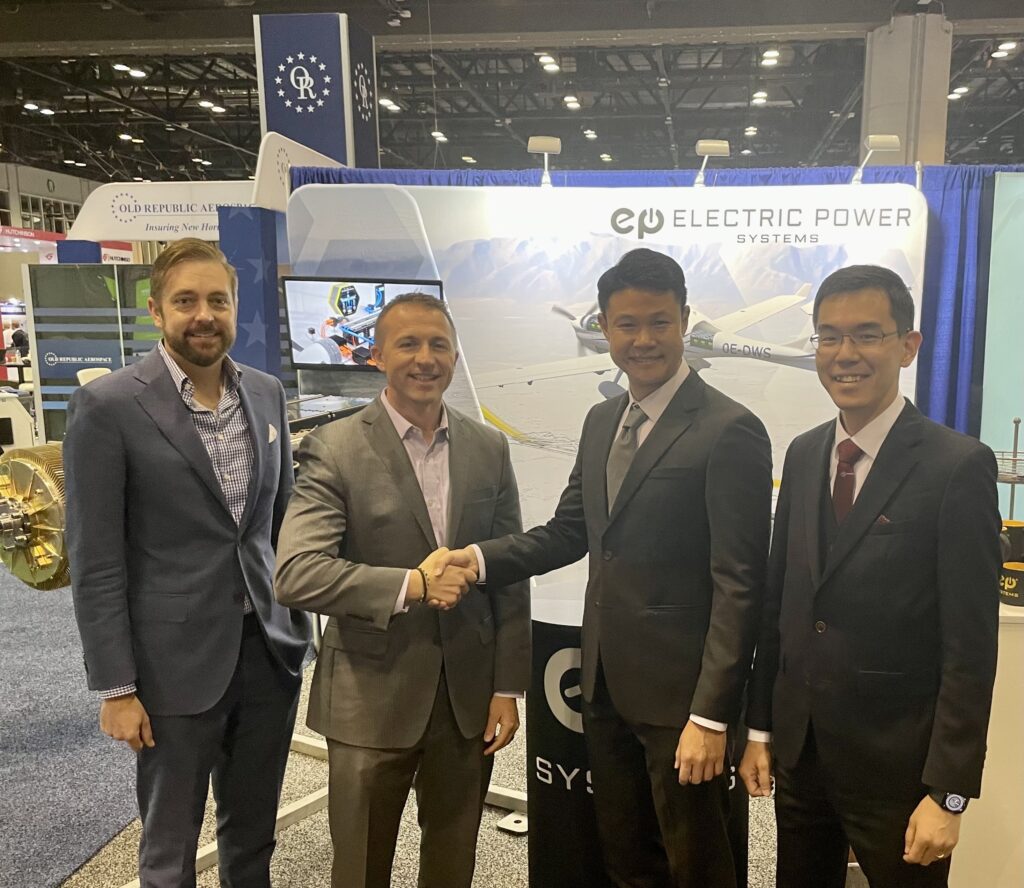
Plana recently chose Electric Power Systems to provide the batteries for its hybrid-electric vertical take-off and landing aircraft. (Photo: Jessica Reed)
Plana, a company based in South Korea developing hybrid-electric vertical take-off and landing (eVTOL) aircraft, announced this week that it has selected an electric powertrain supplier. Plana signed a Letter of Intent (LOI) with Electric Power Systems to deploy its battery systems for Plana’s eVTOL aircraft.
In an interview with Avionics International, Jinmo Lee, Chief Product Officer at Plana, and Nathan Millecam, CEO of Electric Power Systems (EPS), both remarked on the new agreement.
“We’re glad to have an LOI for the battery systems from EPS,” said Lee. EPS offers “well-made battery systems for aviation,” he added. “We look forward to integrating this system into our hybrid eVTOL development.”
Millecam stated, “We’re very excited to work with Plana. We really love their aircraft; they’ve built a great team in Korea, and it’s nice to see international partners and international projects that we can enable. It’s a big deal for us.”
Plana’s aircraft is designed to carry four to six passengers in addition to a pilot. Lee mentioned the company’s latest fundraising efforts, saying, “We closed our pre-Series A funding very recently, and we have gathered accumulated funds of about $10 million.”
“We are thinking of starting the next [round of] fundraising in the second quarter of next year,” added Lee.
He noted that they are currently expanding their team with aviation experts as Plana continues to work on building its half-scale prototype. The prototype should be completed by the end of 2023, Lee shared.
In addition to Plana, other customers of EPS include NASA, Boeing, the FAA, and Safran. In September, EPS was chosen by the company Ampaire to supply propulsion battery packs for Ampaire’s hybrid-electric Eco Caravan aircraft.

Ampaire’s Eco Caravan model (Photo: Ampaire)
EPS was also selected as the first development partner for Supernal’s eVTOL. The partnership with Hyundai Motor Group’s Supernal was announced in July. The teams from both companies will collaborate to develop and produce batteries for eVTOL aircraft and to enable the introduction of commercial flights with eVTOLs.
Millecam shared with Avionics that EPS has completed the initial round of de-risk testing for their EPiC system, and they are on track to certify the module in mid-2023. “De-risk testing allows us to declare the module safe for manned flight,” he explained. “We’re targeting our final critical design review by the end of this year.”
Lee spoke to the many challenges facing the advanced air mobility industry: “Technology, regulations, social acceptance, and infrastructure” are the main ones. “The number one priority of this industry is the safety of the passengers who are using this mobility,” he said. “That could be the most important and challenging part—making every component of aircraft integration to pursue this objective.”
Millecam views certification as the nearest-term challenge, he said. “One of the results of the 737 MAX is that regulatory agencies are looking over each others’ work and scrutinizing certifications much more than they have in the past.”
That scrutiny is actually a good thing for the aviation industry and the advanced air mobility space, he explained. The challenge is establishing consensus between agencies and various organizations.
“We feel like we’re in a very strong position with certifying with the FAA and also have a number of customers in Europe as well as in Asia. That very much helps drive the consensus,” Millecam said, “because every country is very motivated to get these projects certified and to help this industry transition from development and startups to a full-fledged, production-oriented industry.”
The next big challenge for those involved in advanced air mobility will be scaling up manufacturing, he remarked. EPS will need to be able to build high-quality batteries designed for aviation, and to manufacture at the scale of the automotive industry, without sacrificing safety or quality standards. The ability to manufacture “at low cost, at scale, and consistently is a whole new challenge for the aviation industry,” he said.