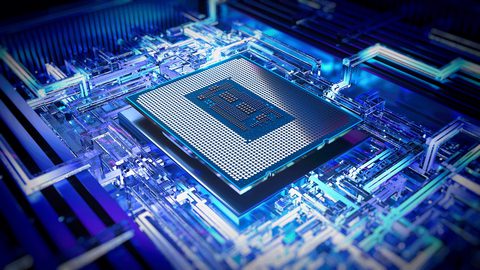
Pre-integrating hardware and software components can alleviate the complications surrounding multi-core processor certification. (Photo: Intel Corporation)
After decades of relying on single-core processors to power everything from flight controls to cockpit instrumentation panels, it appears avionics manufacturers are ready to embrace multi-core processors in the hopes of saving Size, Weight, and Power (SWaP) and achieving greater efficiency. But the move toward multi-core processors comes with significant concerns and complications that have impeded the ability to certify the technology.
Here, we will look at the complications surrounding multi-core processor certification and how pre-integrating hardware and software components can alleviate those issues, resulting in more efficient certification processes and safer equipment.
Multi-core complexity creates certification challenges
The concept of determinism dictates that every event has a cause. In compute terms, a two-core processor might have different cores sharing the same cache, each with its own cause.
Things can get complicated when the two converge. For example, a core handling non-safety-critical tasks could accidentally lock the cache, preventing the second core—which handles safety-critical tasks—from performing its functions. The more cores in the processor, the greater the chances of multi-channel interference between the cores.
It’s difficult to predict when or if this will happen, and that has made certifying multi-core processors historically challenging. Certification of any technology depends on that technology behaving in reliable and predictable ways. This is especially important in avionics, which holds strict Design Assurance Level (DAL) standards, particularly DAL-A and DAL-B.
Unfortunately, multi-processing has not traditionally been reliable or predictable, at least as far as avionics certification goes. Avionics manufacturers normally must run multiple cycles to determine possible failures, gather and parse swaths of data, and more—a time-consuming process.
Now, there are tangible and more efficient solutions built on pre-integrated hardware and software components, making multi-core interference much less of a concern. With these integrations, avionics manufacturers can more easily gather safety certification data from the hardware, creating a certification process that is efficient, faster, predictable, and safe.
Hardware integration addresses challenges and expedites certification
There are a few specific ways integrating hardware and software helps avionics teams address their determinism challenges and expedite their certification processes.
First, avionics manufacturers have typically needed to perform their own analysis and characterization of the processor chips they’ve purchased from vendors. That’s because most chips are provided with low-level data, requiring avionics teams to perform extensive due diligence to ensure that the chips’ data corresponds with DO-254 level safety standards.
Conversely, chips designed with both hardware and software in mind, and that already include this information, take much of the onus off avionics teams. They no longer need to concern themselves with combing through multitudes of data to ensure the chips comply with required safety standards and ensure critical workloads do not get preempted. CoreAVI and Intel are working together to help with the product developer’s bottom line. Both companies recognize how important aviation safety is for all and supporting avionics customers’ requirements. The benefits of time and engineering resources savings in platform safety certification are clear. A pre-integrated solution reduces system integrators’ risks and allows a quicker time to deployment.
Second, most multi-core processors include generic bootloaders or a Basic Input/Output System (BIOS), of which avionics manufacturers may only use a subset of specialized features. Since the cost to certify a single line of code can be extraordinarily high, avionics teams need to go through the systems and remove any unnecessary code that does not require certification. They must also ensure that codes comply with the parameters around DO-178C, which requires that each line of code have a purpose (or, again, cause).
Bootloaders and BIOS that have been pre-certified and manufactured to provide avionics manufacturers with only relevant code allow avionics teams to streamline their multi-core certification processes. A board support package with just enough data to get the system up and running is an example of a system that uses an integrated hardware and software approach to provide manufacturers with precisely what they need and no more.
A look forward
Improving and accelerating certification processes is only the beginning of a series of potentially game-changing use cases that could result from the use of multi-core processors in avionics.
Multi-core processing will play a key role in making air transportation both smarter and safer. Applications like artificial intelligence (AI) and machine learning (ML) depend on multiple cores to be able to process information, such as wind speed and direction, from various sensors. This information is turned into actionable data that human pilots and self-piloted aircraft can use to make real-time decisions while in flight.
With enough data, a single pilot can fly without the need of a co-pilot and still effectively manage her journey; a drone can accurately drop off a package at a person’s doorstep; or the pilot of an air taxi can maximize the craft’s flight distance.
But these use cases also need the right amount of processing power to manage the data. Multi-core processors built with pre-integrated hardware and software deliver that power, creating greater efficiencies in certification and opportunities for the future.
This article was written by Debra Aubrey, Technical Product Marketing Manager, Federal and Aerospace, Intel Corporation.