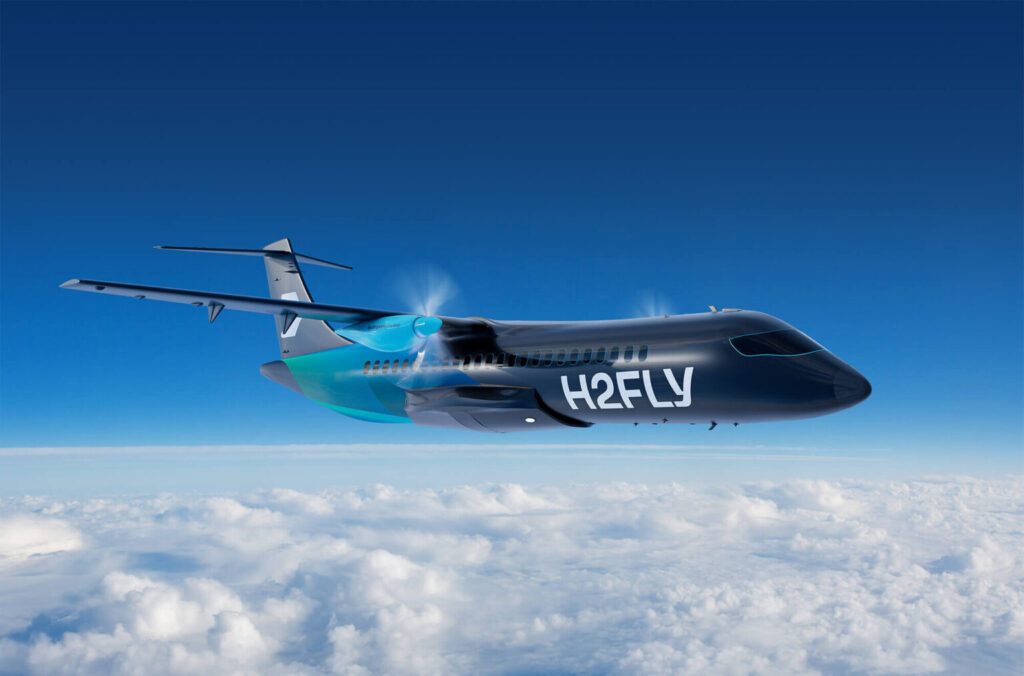
“Our H175 is the first fuel cell system that is purpose-built for aviation and will be a seminal cornerstone to bringing this technology to the required readiness level for the market.” – Josef Kallo, CEO and co-founder of H2FLY (Photo: H2FLY)
H2FLY, a developer of aircraft hydrogen-electric powertrain systems, recently unveiled the latest iteration of its exclusive fuel cell technology, the H175. This modular power unit is specifically designed for application in commercial aircraft, boasting exceptional performance capabilities.
The H175 program will deliver a range of fuel cell systems that can be expanded to power hydrogen-electric aircraft in the megawatt-class category. The technology is suitable for aircraft with up to 80 seats. H2FLY manages the comprehensive development, integration, and testing of the hardware and software for the fuel cell systems.
While operating at flight altitudes of up to 27,000 feet, the H175 systems can provide their full power range. This represents a significant milestone on the journey from initial flight demonstrations at lower altitudes to real-world implementation in commercial aircraft.
H2FLY plans to conduct flight demonstrations of the first-generation H175 system later in 2023. The company also intends to integrate H175 fuel cell systems into a Dornier 328 demonstrator aircraft as part of the German government’s 328 H2-FC project. The project, funded by the German Ministry for Economic Affairs and Climate Action (BMWK), is a collaborative effort aiming to develop and test a megawatt-range hydrogen-electric fuel cell system.
Josef Kallo, CEO and co-founder of H2FLY, shared in a statement to Avionics International that the H175 power modules can be combined in parallel or in series. “This allows us to scale up the total output power and achieve outputs of over a megawatt,” he explained.
Some of the specific advantages of the next-generation H175 system include optimized packaging and a proprietary control system from H2FLY. The control system allows for the use of the fuel cell stacks at high power while maintaining durability.
“We use the latest generation of components and fuel cell stacks,” Kallo said. “We get maximum power output at aviation operating conditions, which enables us to fly at altitudes of up to 27,000 feet (Flight Level 270) and therefore paves the way to commercialization.”
When asked about the challenges involved in using liquid hydrogen with fuel cells, he pointed to the process of refueling. “The lack of permanent and purpose-built infrastructure at airports means that we have to rely on individual and temporary solutions, which often cost a lot more. We hope for a standardized solution for hydrogen infrastructure at airports,” he remarked.
In addition to the team’s plans to demonstrate the H175 system in flight tests later this year, they are also anticipating a demonstration of a complete liquid hydrogen fuel cell powertrain in flight with the HY4 aircraft in the summer.
“We solved the challenge of conditioning liquid hydrogen, leading to the very efficient use of hydrogen in the fuel cell,” added Kallo. “We look forward to demonstrating the full functionality of the liquid hydrogen fuel cell powertrain during flight this summer.”
He commented that, from his perspective, truly sustainable air travel requires fuel cell powertrains. “Using fuel cell systems in aircraft only emits water vapor,” he explained. “Other solutions to decarbonize aviation, e.g., sustainable aviation fuels (SAF), still emit greenhouse gases. Furthermore, the production of SAF [is] highly inefficient as a result of energy usage during the production process.”