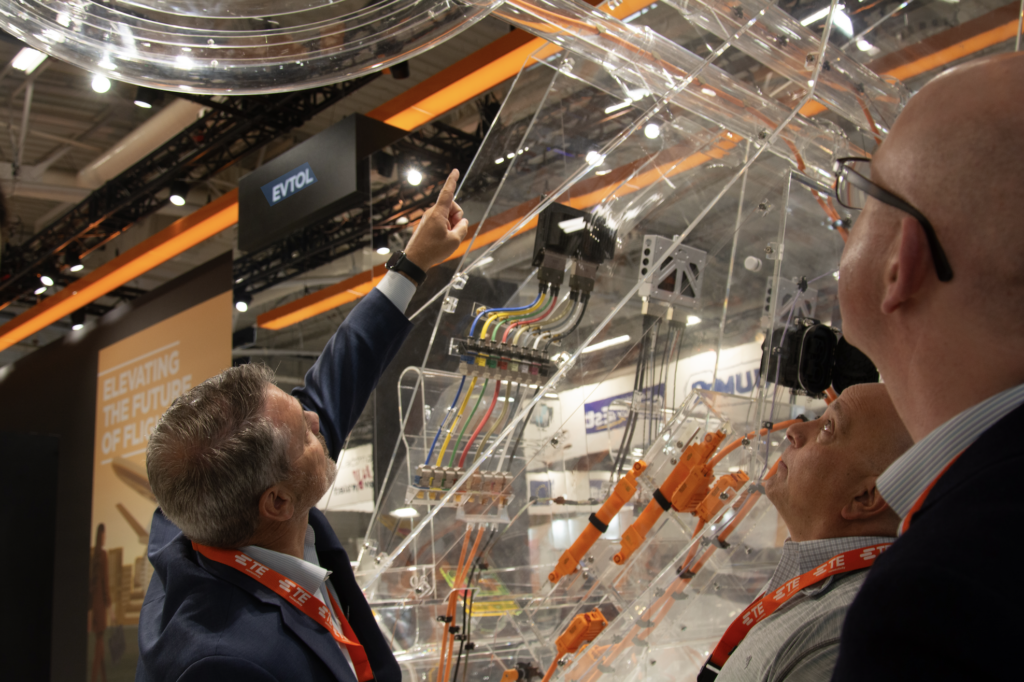
Take a closer look at the latest innovations in LEO satellite technology, power distribution for electric aircraft, and fiber-optic distributed networks for improving in-flight connectivity. (Photos: TE Connectivity)
Matt McAlonis, Fellow, Aerospace of TE Connectivity, recently talked with Avionics International about the company’s innovations in aerospace and LEO satellite technology. He highlighted their commitment to reliability, high-speed connectivity, and efficient designs to meet the evolving demands of the aviation and satellite industries.
The growing demand for digital connectivity in aircraft has led to an increased need for components that manage content connection and safety systems. “You have so much more content that has to be connected, and so many more people that want to be—and expect to be—connected,” McAlonis said.
He noted that modern aircraft designs, such as the A350, use carbon fiber composites, which necessitates specialized electrical connection systems. TE Connectivity is one provider of these systems.
“As there’s more and more tech that goes inside [the aircraft], you need more power,” he explained. “We have to be able to connect the generator in either the APU or on the engines with our power cables.”
TE Connectivity works with its customers to ensure that their products are weight-optimized as well as efficient and reliable. “These are harsh environments, especially when you try to get things off the ground,” he said. “You can’t just pull over like you can in a car. The airplane has to be reliable.”

McAlonis also discussed power requirements in the context of advanced aircraft that use electric propulsion. The emerging industry of eVTOL and hybrid aircraft has introduced new propulsion systems that have significantly higher power requirements than traditional aircraft systems.
“If you run more amps, you need thicker cables with copper that can handle the amperage,” he said. “But power is a function of current and voltage. If you’re limited in space with the amount of power cables and weight—because you have to get lift and fly—then the other lever you can tweak is voltage.”
However, increasing the voltage brings new challenges. Ensuring that their products (especially those related to power distribution and switching) can handle these increased power demands safely and reliably for next-generation aircraft is a priority for TE Connectivity.
“Designing practical advanced air mobility ‘air taxis’ or eVTOL vehicles poses a new and complex set of challenges,” McAlonis wrote in a case study titled, “Imagining the Future of Flight.” Some of these challenges include:
- “Navigating as low as 500 feet over 50-mile hops across a cityscape, which imposes new demands on air traffic control, sensor, data processing and connectivity.”
- “Charging batteries for eVTOL aircraft must be done in minutes instead of hours to make commercial electric flight financially viable. Special cables, contactors, and switches can handle high voltages, amperages, and temperatures encountered during fast charging.”
During the recent interview with Avionics, McAlonis described how fiber-optic distributed networks can improve the passenger’s in-flight entertainment and connectivity (IFEC) experience. “Fiber optics are a technology that uses photons instead of electrons” to transmit data, allowing for extremely high-speed and high-bandwidth communication. This is essential for in-flight entertainment with multiple passengers accessing diverse content.

Compared to traditional copper cable systems, fiber optics are lighter and more compact, reducing weight and saving space—crucial factors considering the cost implications of fuel consumption.
The utilization of fiber optics in aircraft not only enhances the in-flight experience but also helps in reducing fuel costs by minimizing the weight of the communication infrastructure. “It helps to save space and weight, and it’s enabling more and more data,” he shared.

TE Connectivity develops components to support Low Earth Orbit (LEO) satellites. LEO satellite networks provide enhanced coverage, redundancy, and connectivity to remote areas by allowing users to maintain consistent satellite visibility.
The satellites employ phased array antennas for user connectivity, routing information through satellite processing systems. TE Connectivity produces the wiring for the solar panels that power these satellites, which must endure harsh conditions like radiation and temperature extremes due to rapid orbital cycling.
“The cables are connected to the solar cells by solder joints or connectors, and all that has to be designed for reliability,” according to McAlonis.
“A lot of satellites have to fit into the payload area of the rocket,” he added. “So our products have to be miniaturized and able to be folded up sometimes. All of that matters: getting it weight optimized, shape optimized, and electrically optimized.”
