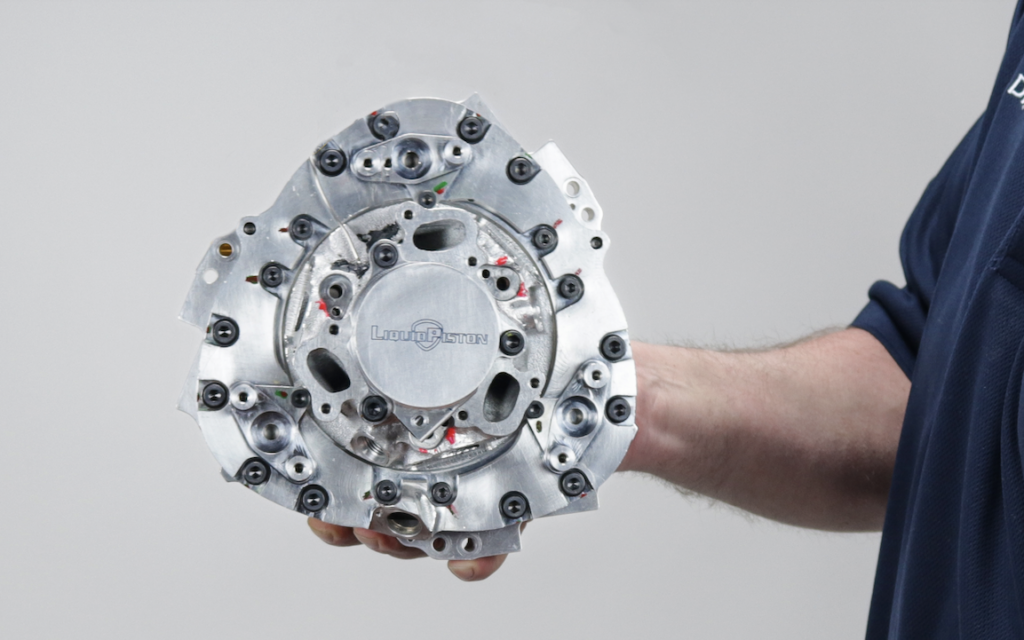
LiquidPiston recently introduced its latest-generation engine, the XTS-210. (Photo: LiquidPiston)
The short answer is yes: innovative internal combustion engines, especially in combination with batteries, can and will play a crucial role in decarbonizing aviation for small aircraft, urban air mobility applications, group 2 and 3 (50–1200 pounds) unmanned aerial systems, and urban air mobility vehicles. (For combustion turbine engines in larger passenger aircraft, the future lies more in the fuel than the engine design at this point.)
In fact, even while automotive applications push toward full electrification, sustainable aviation applications will likely include hybrid electric propulsion systems that include a battery and a range-extending internal combustion engine (ICE) for the foreseeable future.
Let’s take a look at why that is and what sustainable ICE applications might look like in aviation for small and mid-sized aircraft.
Batteries have an energy density problem
On the ground, fully electric vehicles powered by batteries can work. They’re on the road already and steadily growing in number—a key achievement as we decarbonize transportation. The biggest problem fully electric automobiles face today is one of infrastructure: we need to greatly increase the number of charging stations, as well as upgrade the grid to power those home-based and public charging stations, in order to facilitate a more complete transition to EVs.
For flight applications, the main challenge with batteries is not infrastructure but weight. Aircraft need power not only for horizontal flight but also for lift. The heavier the plane, the more power and fuel are required to get it into the sky. Batteries are heavier than jet fuel and take up more space. And while researchers are working steadily to improve the energy density of batteries, jet fuel today has about 30 times more energy per pound than the most advanced lithium-ion batteries. Even a 2x or 3x improvement of battery energy density—which we may well achieve in the coming decades—won’t bring them within range of jet fuel.
The good news for everyone is that decarbonizing flight isn’t an either-or proposition. That is, although aircraft that rely solely on battery power may have flight time and payload limitations in the short-to-medium term, aircraft that make use of hybrid electric power systems can excel in a variety of scenarios while also reducing carbon emissions.
How hybrid aircraft are pushing decarbonization forward
As the cofounders of French startup Ascendance pointed out in a May interview, “Hybrid technology is the only short- to mid-term answer if you want to keep range while decarbonizing.”
Toyota made a related point (albeit for the automotive space) in a memo sent in April, noting that the raw materials required to produce a single long-range EV could instead produce six plug-in hybrid vehicles or 90 hybrid electric vehicles—and that the lifetime carbon reduction of those 90 vehicles would be 37 times greater than that of the single EV.
This is a crucial concept to keep in mind as we decarbonize flight: what we do between now and the future state of full decarbonization matters a lot.
Today’s batteries are too heavy to feasibly power passenger or commercial flights. But hybrid propulsion systems can do both, and they can cut carbon production significantly while doing it.
For example, there are currently fully electric VTOL aircraft capable of tens of minutes of flight. While those aircraft will likely develop compelling applications, battery life will be a significant limiting factor.
Hybrid flight applications offer an exciting contrast. In the Hybrid Electric X-Engine (HEXE) power system that LiquidPiston is currently testing in VTOL applications, for instance, we combine a battery with a rotary engine and a motor/generator in a parallel architecture. In a feasibility study conducted for the Army, this structure enabled us to extend total flight time by 48 percent (from eight hours to 11.8) over a gasoline 2-stroke engine.
What’s more, the hybrid propulsion system makes it possible to use combined power from the engine and the electric motor simultaneously to increase total thrust produced. In our study, we found that increases in velocity for short duration “sprints” can be as much as 40%, and climb time can be reduced, as well.
Embracing hybrid propulsion systems as we decarbonize flight also offers another key benefit: an antidote to range anxiety. When an EV runs out of charge before you reach a charging station, it’s annoying. The analog for a fully electric aircraft amounts to something much worse – especially in urban air mobility (UAM) applications.
A hybrid system can offer redundancy, with an ICE onboard that can both serve as backup power and charge the battery mid-flight. When we think about not just what’s possible but also what’s acceptable to consumers, i.e. what will convince them to step onto a lower-carbon aircraft this is a crucial part of the equation. It’s far better to slash carbon emissions with the technology we have today (or that we’ll have in three years) than to sustain the status quo until sometime in the distant future we’re able to completely eliminate carbon from flight.
We can improve ICE efficiency, too
When we accept that the future of aviation is hybrid and that internal combustion engines have a role in that future, we can then focus on optimizing the performance of both the batteries and the engines themselves.
The latter consideration—optimizing engines—has been largely missing from much of the conversation about decarbonizing. But it’s a hugely important component.
I mentioned research dedicated to improving batteries’ energy density. We need similar innovation for engines, finding ways to create power with lighter, more efficient engines so that aircraft have more of a “budget” for battery weight and fuel. We need engines capable of operating on sustainable fuels and we need renewable ways of producing those fuels.
We’re making progress: last fall, Australian researchers announced a prototype that produces hydrogen fuel of 99 percent purity via solar power. At my startup, LiquidPiston, in addition to the 10-horsepower HEXE, my team and I have developed a 25-horsepower X-Engine that’s five times smaller and lighter than a comparable diesel piston engine. When mature, it is expected to be 30 percent more efficient and capable of running on hydrogen and low carbon “efuels.” Our X-Engine platform is also scalable up to about 1000 hp.
The bottom line? An ICE architecture that is focused on compact hybrid power systems, that has optimized thermodynamics for increased fuel efficiency, and that has multi-fuel capability is in a position to power the aviation energy transition and decarbonization.
The future of flight is hybrid—in every sense
There’s no question that we need to electrify transportation to meet carbon emissions targets. In aviation applications, the most practical path to decarbonization is embracing hybrid, in the broadest sense of the word. We need not just hybrid propulsion technology but also hybrid energy sources, hybrid energy conversion options, and hybrid fuel distribution strategies.
We need better grid capacity and resiliency and electric charging infrastructure in different countries and regions within those countries—as well as a mix of fossil fuels and biofuels. We need a mix of aircraft types and business models. A dynamic mix of market demand, business economic opportunity, and government industrial and environmental policies are stimulating a lot of innovation and experiments in all these areas worldwide.
We need everyone’s skills, ideas, and capacity for innovation—because we need to build a future that works better for all of us.
Alec Shkolnik is co-founder & CEO of LiquidPiston, which is a leading developer of combustion engines and hybrid power solutions that are scalable, compact, and capable of utilizing efficient fossil or renewable fuel. Alec has a PhD from MIT’s Computer Science and Artificial Intelligence Laboratory, where he was an NSF Graduate Research Fellow and a postdoctoral researcher.